Heat Management in Airports
In the ever-evolving world of aviation, sustainability is no longer an option—it’s a necessity. Airports across the globe are under increasing pressure to reduce their environmental impact while enhancing passenger comfort and operational efficiency. Super Therm®, a globally proven heat-block insulation coating, is leading the charge in sustainable innovation for the aviation sector.
Why Super Therm® for Aviation?
Super Therm® is not just another coating—it’s a game-changer. Developed in collaboration with NASA, this advanced ceramic insulation coating blocks 96.1% of total solar heat, eliminating heat load transfer to interiors. For aviation hubs, this means significant energy savings and enhanced passenger comfort, all while reducing greenhouse gas emissions.
- Harry Reid International Airport – Las Vegas
- Tucson International Airport: A Model of Energy Efficiency
- US Air Force Renewable Energy Symposium
- Chengdu Shuangliu International Airport, China
Harry Reid International Airport loves Super Therm – Las Vegas
Super Therm® Reduces your energy use, protects passengers and reduces CO2
The SPI Coatings system was used at Harry Reid International Airport Las Vegas, USA for heat load protection and improved passenger comfort for boarding bridges in the hot environment.
Las Vegas has an average summer temperature of 40°C and the steel bridges can get very, very hot with minimal air flow up to 90°C. The Harry Reid International Airport tested various competitive products and Super Therm® Ceramic Heat Block coating outperformed the closest competing product by more than 6°C (20°F) on the bridge roof. The Harry Reid International Airport tested various competitive products and Super Therm® outperformed the closest competing product by more than 6°C (20°F) on the bridge roof. Super Therm® has been tested to block 96.1% of the heat.
Super Therm® was applied at the standard 10 mils (250 microns) dry thickness compared to 30 mils (0.75mm) of the closest competitor and surpassed them by 6°C (20°F) which allowed for more comfortable environment and more efficient air conditioning.
Enamo Grip 5000 clear was applied after the Super Therm® to produce a protective coating. Enamo Grip 5000 is a two component polyester high solids coating for protection against vapours, acid rain, and other harsh chemical environments while giving a car-like finish and UV protection. It can withstand Skydrol® hydraulic fluids used in aircraft when applied to flooring.
Read the Cool Article
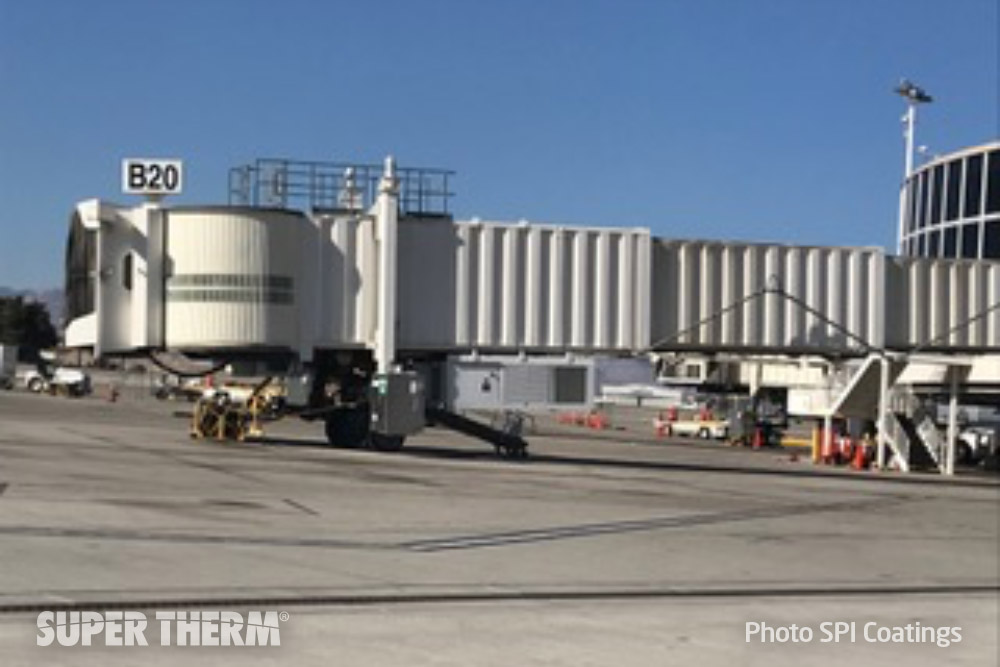
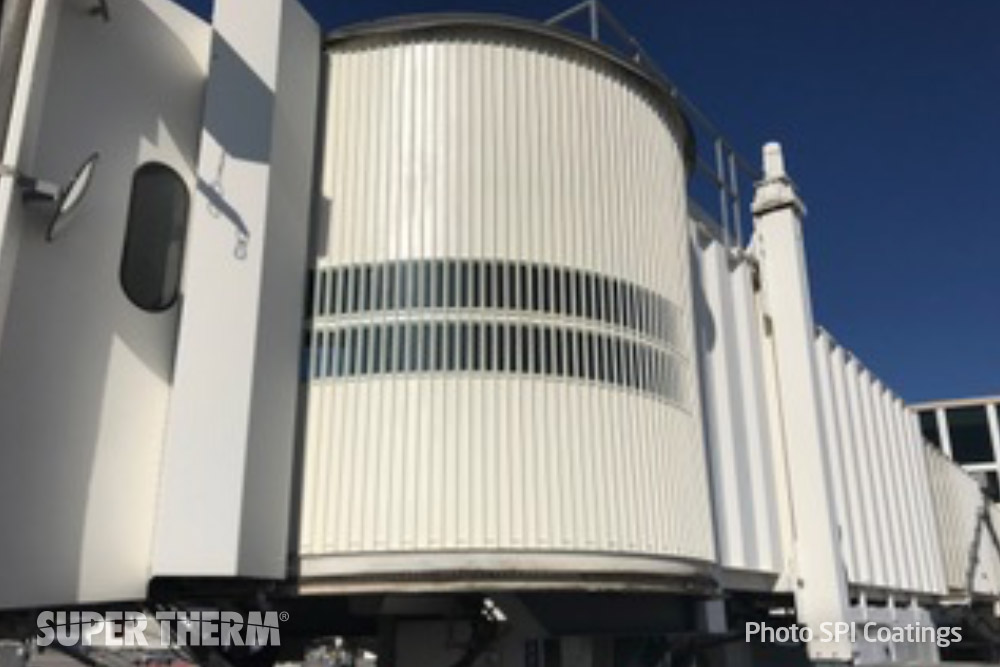
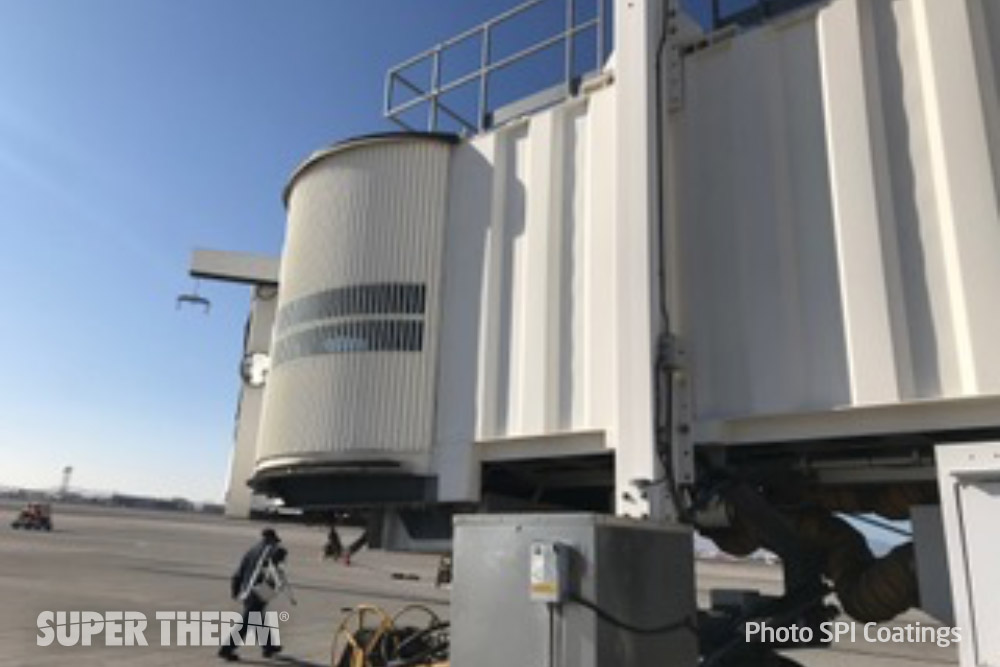
Read the Cool Article
Tucson International Airport: A Model of Energy Efficiency
This simply means that the SUPER THERM® made a 40% reduction in the A/C costs. From the ENERGY UTILITIES companies, the A/C portion of a total energy bill is 55% which when calculated on the 22% savings of the total relates to the 40% savings in pure A/C costs.
114,240 m2 of roofing coated with the SUPER BASE(HS) / SUPER THERM® System
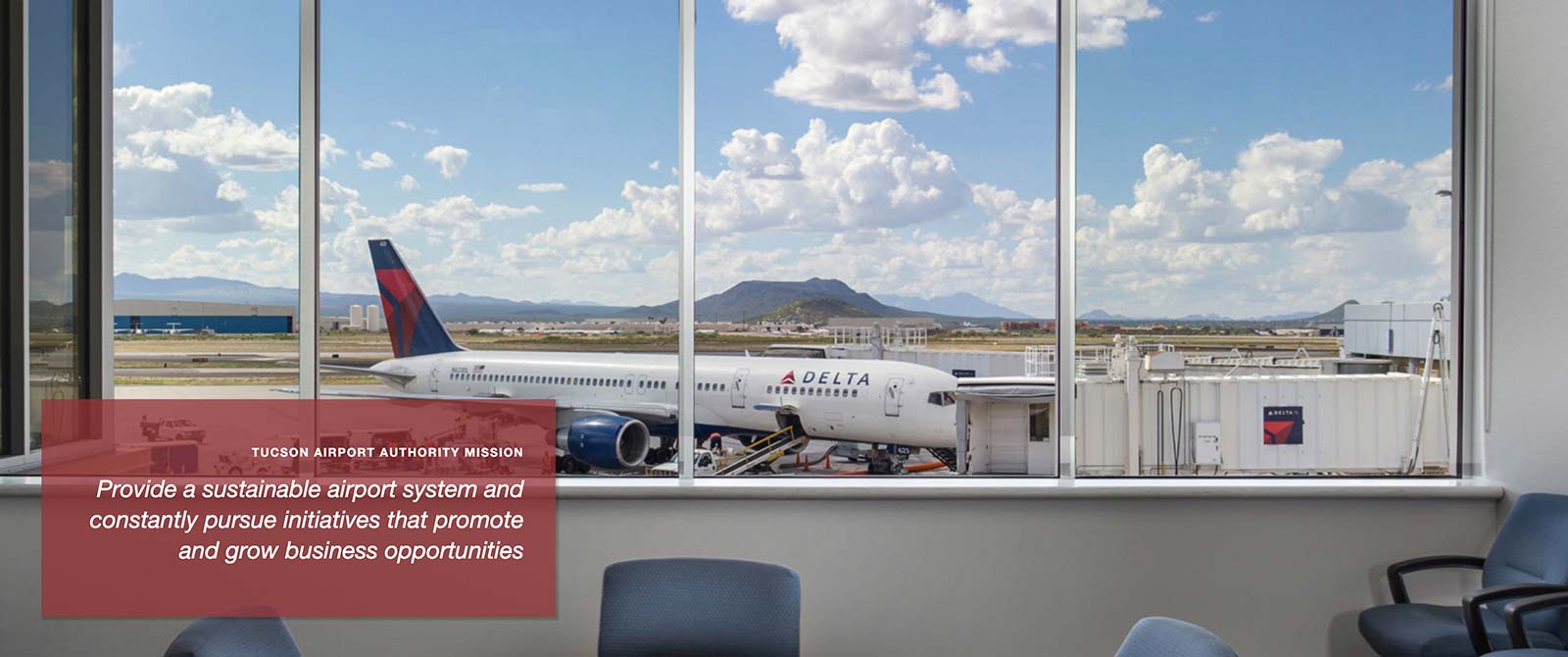
ENERGY AUDIT AND REPORT
Attached are comparisons of our terminal electric bills for August and September 2008/2009. I was trying to get a feel for the potential gains made by the application of the Super Therm® roof coating product that was completed in early August 2009. I calculated the Cooling Degree Days (CCD) for each month and compared the kWh used per CDD for each month. There was a 22% savings in August 2009, and a 8% savings in September 2009.
The temperature change was +3.3°F over 2008 in August and +1.4°F over 2008 in September. According to ConEdison Energy, a 6°F change can relate to a 40% change in A/C cost. With the ambient temperature in 2009 being 3.3°F hotter, this could push the A/C cost up another 20% before SUPER THERM® was applied. Therefore, the savings reported could be 20% to the benefit more than reported.
Chris Wilt
Airport Facilities Manager
Chris Wilt [cwilt@tucsonairport.org]
Note: Results are only for this location, environment, set of weather conditions and cannot be guaranteed to produce the same results in other areas.
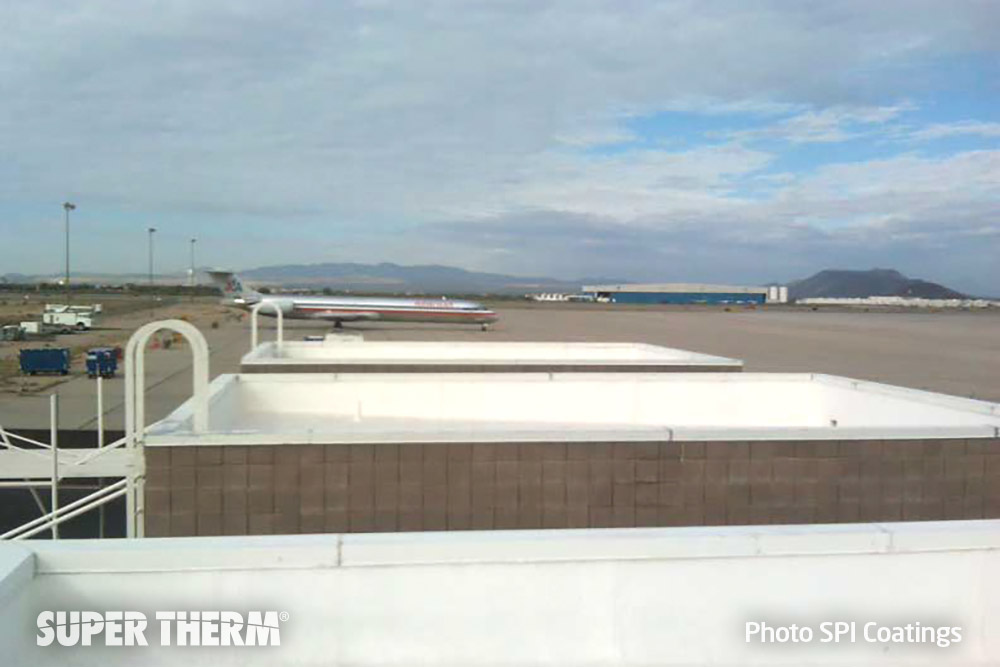
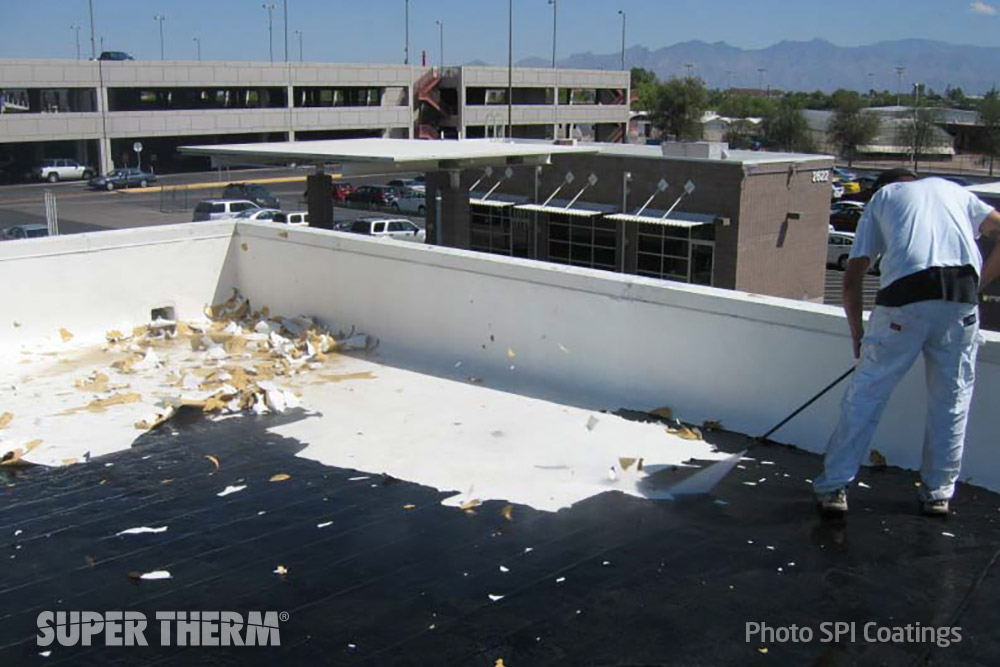
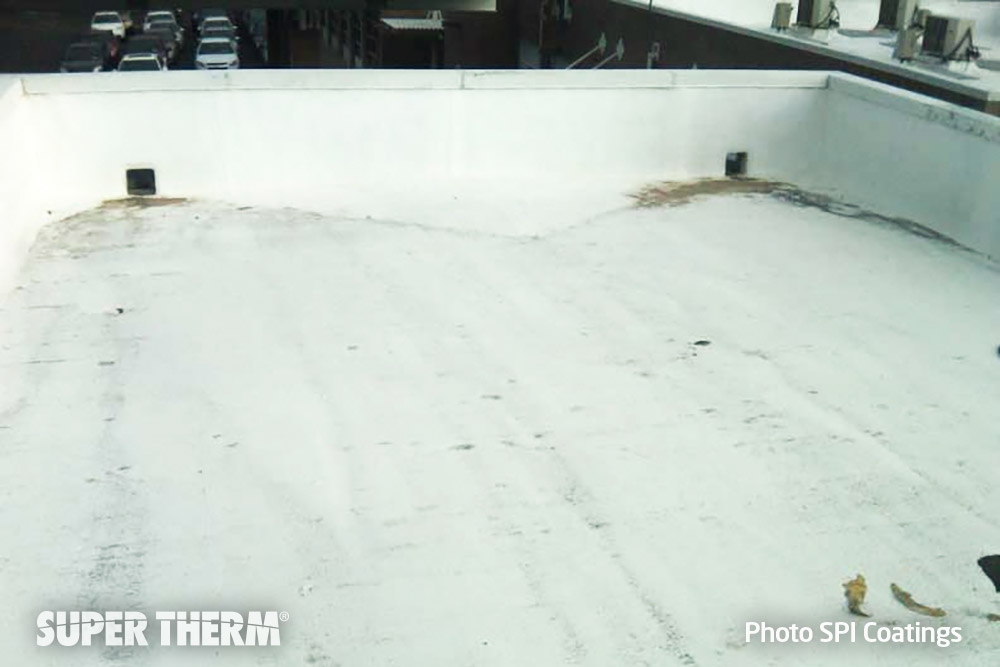
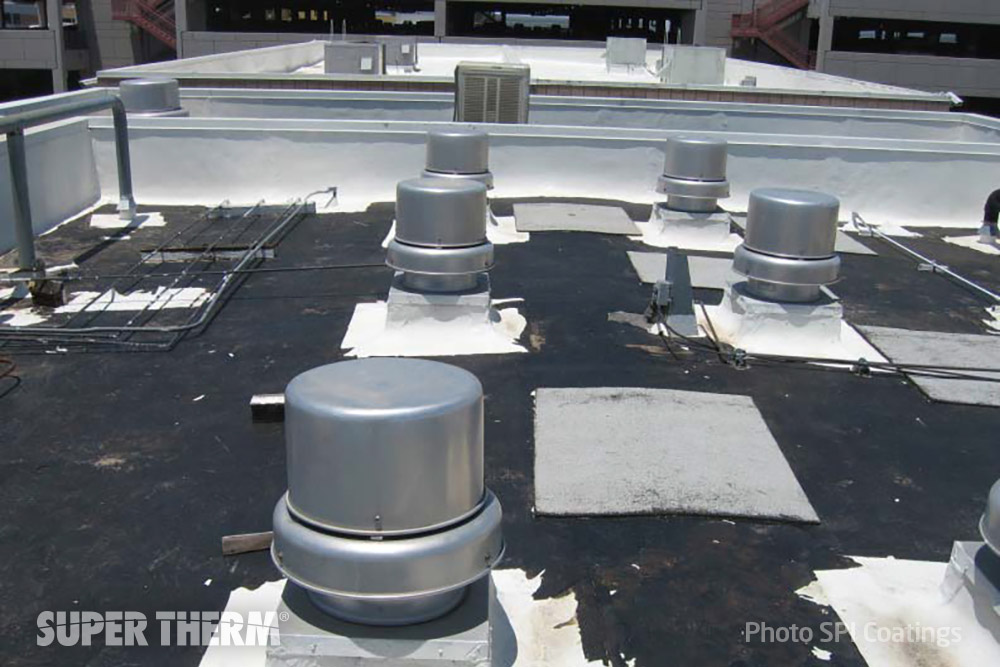
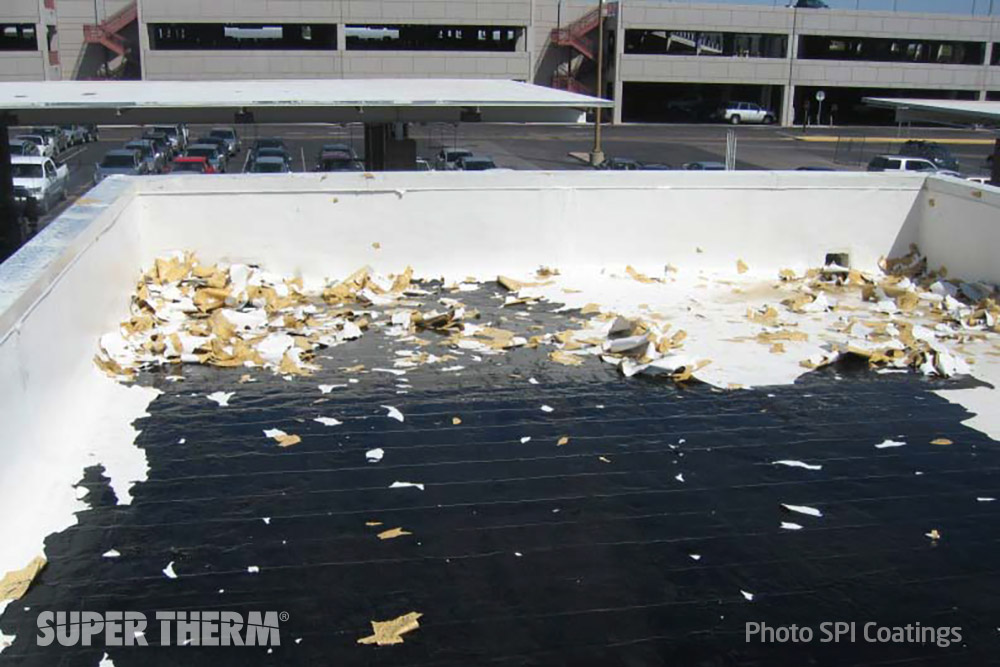
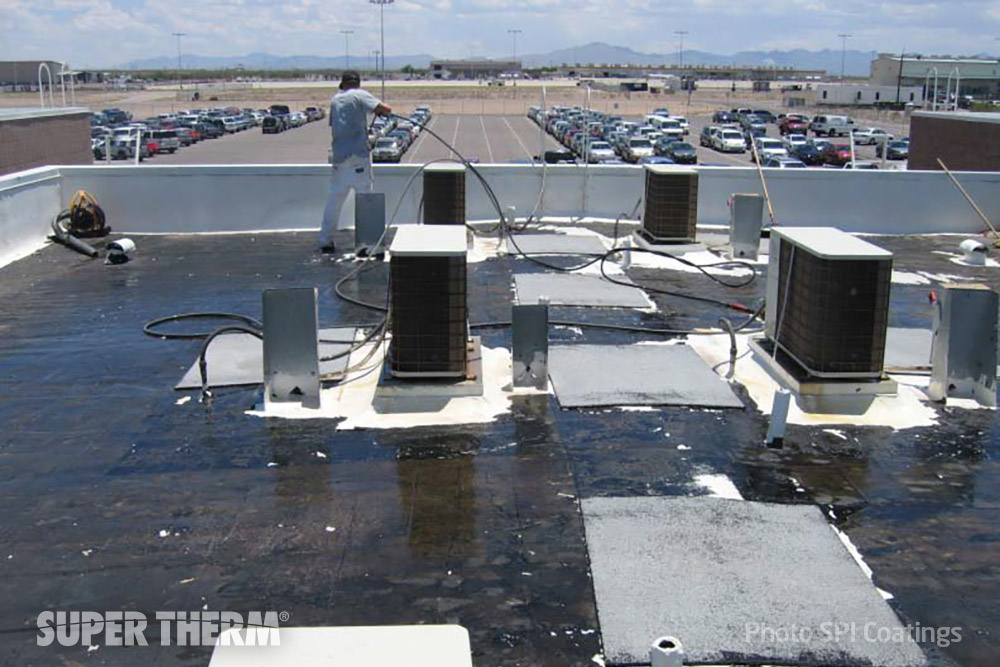
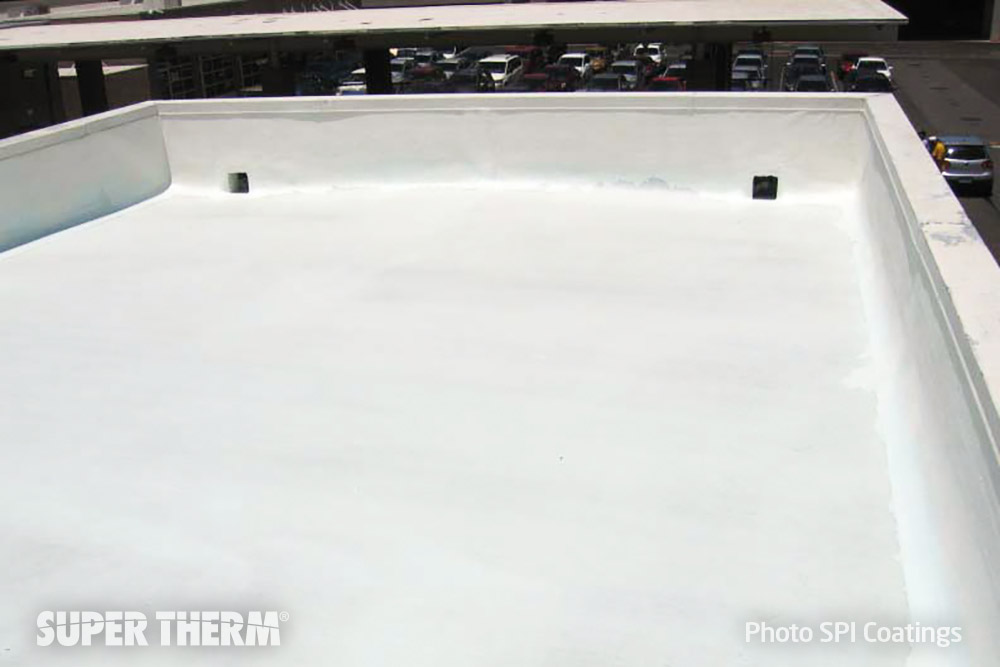
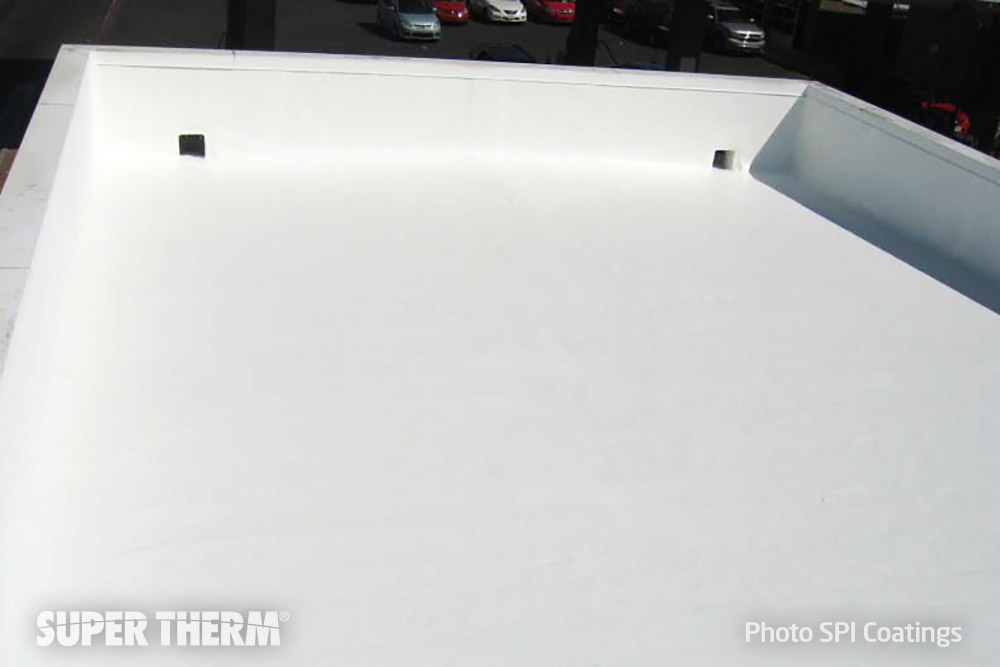
Additional notes below placed by J.E. Pritchett (SPI) concerning the resulting:
- A very important point is that the 22% savings for the airport was on the TOTAL energy bill (lighting, elevators, food facilities, etc).
- This simply means that the SUPER THERM® made a 40% reduction in the A/C costs. From the ENERGY UTILITIES companies, the A/C portion of a total energy bill is 55% which when calculated on the 22% savings of the total relates to the 40% savings in pure A/C costs.
- This is very substantial savings in the A/C cost savings.
- It also means that the A/C tonnage can be reduced to save more money. Equipment savings.
- Run time on the units is reduced which extends their life cycle and saves a tremendous amount of money on replacement or repair of equipment. Maintenance and repair savings.
- Therefore, the cost savings is much more than just the 40% savings for A/C.
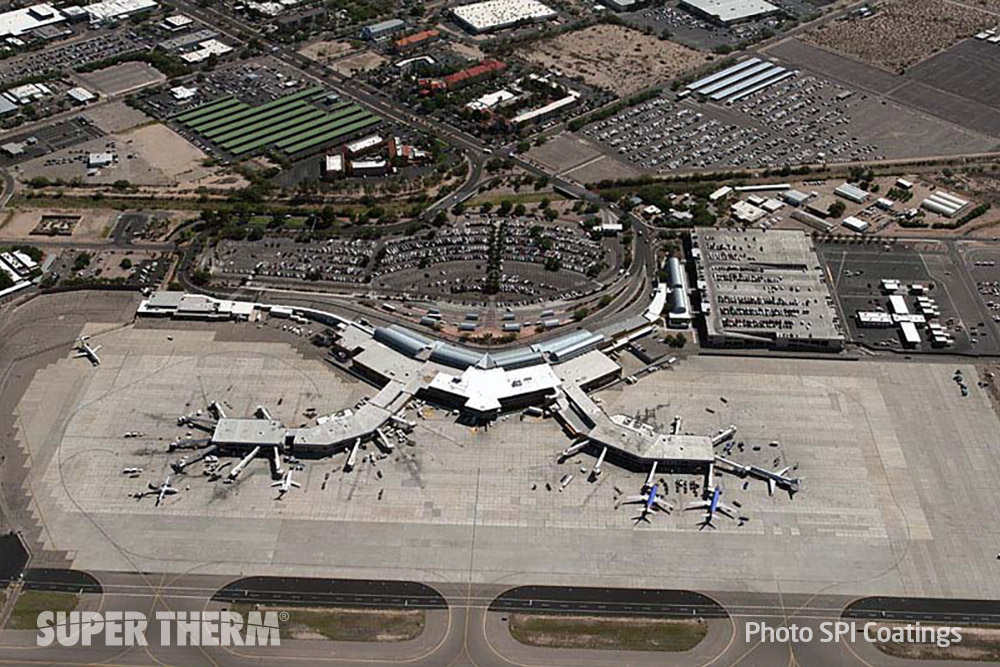


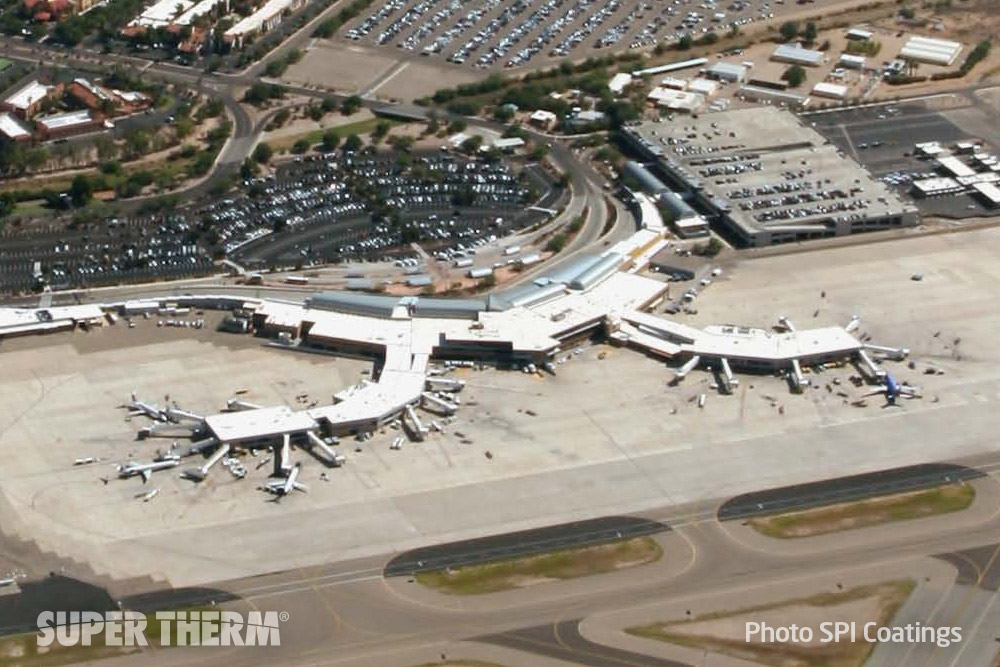
SAVINGS:
With the total utility savings of $22,144 (22%) in August for the total facility and the A/C portion of the total utility being 55%, this relates to a 40% savings in A/C operational cost. The savings are beyond the A/C running cost, the units cycle more giving long life, less maintenance work and less tonnage to take care of the main terminal and wings.
ROI: The total roof area of the terminal is 374,804 sq.ft. applied at $2.10+/ sq.ft. is $787,088. With a cost reduction of $22,144 / month, this results in a 35.54 months return. This average can be a little less and could be much more when taking in the summer months. Point is that after 35 months, this savings amount is now available to offset budget needs without the need to find new funding.
RENTAL CAR WASH BAYS:
The car wash bays were done first, and we had to remove the existing elastomeric coating which was not adhering, was not water proofing and was not insulating.
MAIN TERMINAL ROOF COMPLEX: 114,240 m2
We coated the entire Tucson Airport complex of roofing in Tucson, Arizona.
The attached pictures show the beginning with the centre roof coated and the remaining roofing sections.
There are also additional buildings off site that are scheduled to be coating also.
The roofing is “cap sheet” which is tar paper and this requires SUPER BASE (HS) at 9m2 (100 sq.ft.) per gallon and then overcoated with SUPER THERM® at 9m2 (100 sq.ft.) per gallon.
Other parts of the roofing is PVC or a plastic type material which is weathered but is in good condition and provides good adhesion to accept SUPER THERM® easily at the 9m2 (100 sq.ft.) per gallon.
Preparation was the use of “Simple Green” concentrate cleaner and power wash.
The roof was power washed to wet down, the simple green cleaner was sprayed over the roof and large hard bristled push brooms were used to clean the surface and then the power washer was used to rinse this all off before it dried. The power washer was working behind the push brooms to assure nothing dried before it could be washed off. When the roof surface dried, the SUPER BASE (HS) adhered very strong and tight to the surface.
SUPER THERM® over Chengdu Shuangliu International Airport, China
SUPER THERM® was applied to the terminal roof of Chengdu Shuangliu International Airport and will finish the project in the end of this month. We have tested the temperature in part of the roof, but the difference between uncoated and coated ST is only about 10 ℃. Then we also checked the thickness of ST, and all the thickness are more than 250 microns. According to your experience, would you please tell us what’s the problem?
Answser: The uncoated portion of roof is hot and transferring this heat under the interior side of the coated roof. Until you have all the roof coated, the roof cannot cool down completely to give you the full effect.
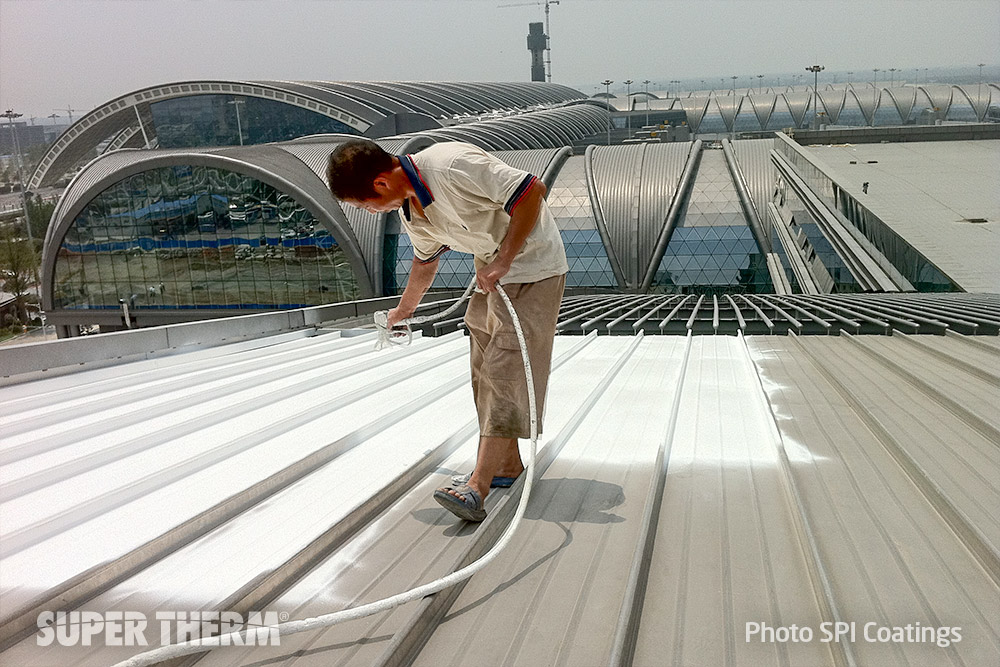
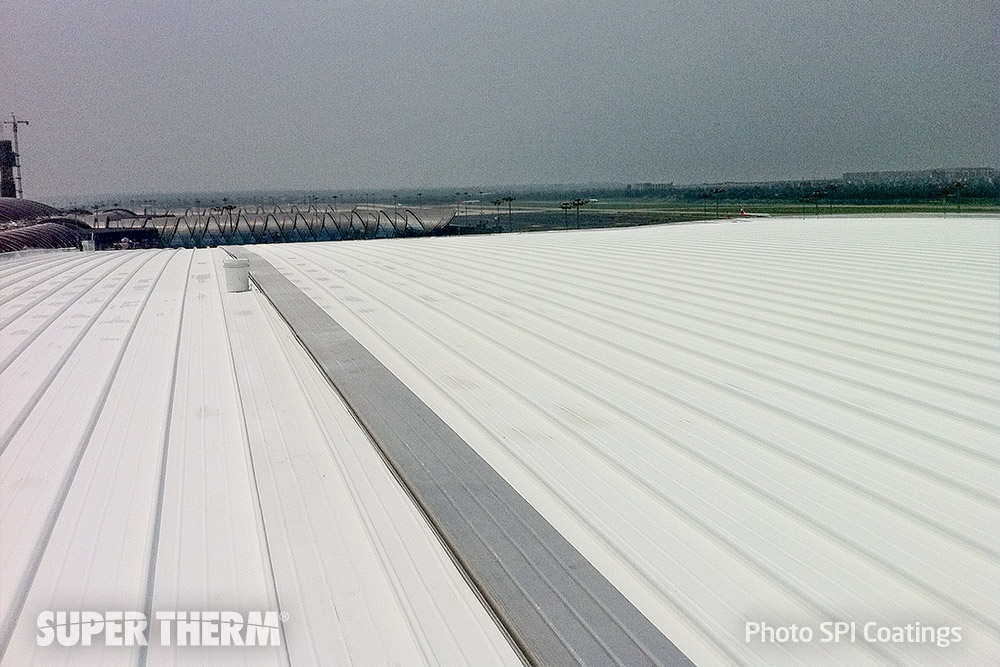
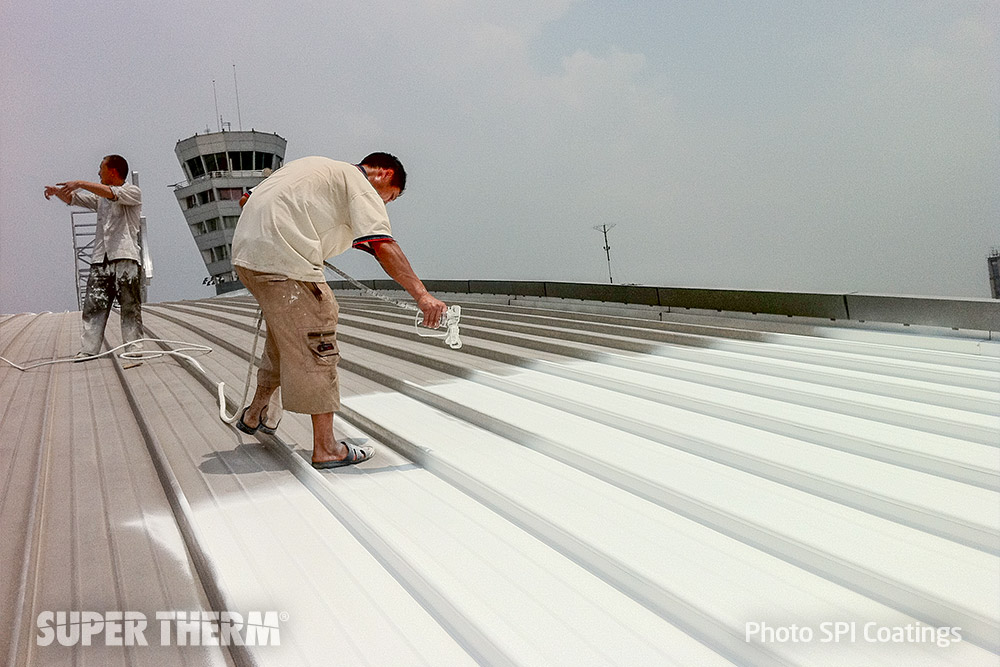
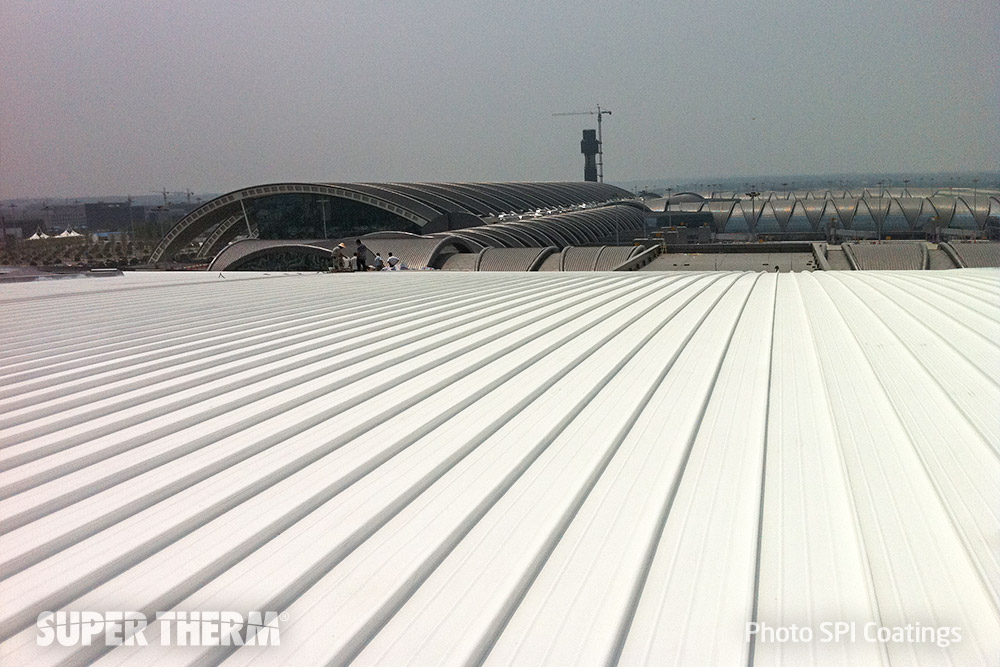