SPI History
SPI has worked with ceramics and industrial coatings for over 35 years
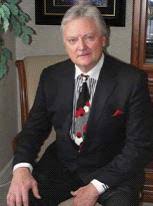
Joseph E. Pritchett (J.E.) is a Ceramic researcher and formulator from Superior Products International II, Inc. USA holding a Bachelor of Science from University of Arkansas and Paint Technology courses from University of Missouri. Graduate studies performed with NASA in Huntsville, Alabama, USA and Ceramic Materials research over the past 35 years. Read J.E.’s Super Therm® White paper.
Single ceramic beginnings
In the beginning since the 1970s and 1980s, the reflective coating concept was very interesting in that using a single ceramic component to reflect surface heat from sun radiation was thought to be the best way to solve heat load. Within a couple of years, this idea that surface reflection would solve any heat load problem on surfaces was discovered to be wrong due to the fact that the coating would become dirty and stop reflecting.
Rethinking ceramic coatings
As the established reflective companies continued to promote and sell this technology, J.E. visited with his Uncle that worked at Red Stone in Alabama that was connected to NASA. He in turn guided him to the engineers that developed and designed the tiles for the shuttle. In working with these engineers for a short time, J.E. found that the ceramics used for the tiles would not work in a coating product when the environment of the compound changed drastically from dry to wet and mixed with other compounds.
Since none of this type of information could be found in any research books, J.E. began to develop and set up Trial and Error procedures to test ceramic compounds in a base coating. The initial thought was that this would take 6 months and the compounds could be found to perform as planned and the coating completed. In the first 6 months, the initial sources were found. The first year, more sources were found. In the fourth year, it was finally decided what to look for in density, crystalline structure and material compound.
Finding the right compounds that will continue to block heat when formulated into a coating is the result of 35 years of R&D to find individual compounds combined together to form a matrix to block radiation waves and detune signals to achieve reduction in “initial heat loads”.
35 years of ceramic coating success
After 35 years and over 4000 ceramic compounds, it was found which compounds actually do work in any environment, mixed with other compounds that will improve the performance, which compounds are good for radiation heat in the ambient atmosphere, which work over high temperature surfaces to block and hold heat and which are good for fire control.
One compound alone could not fully perform the job needed.
It always takes a combination of the correct ceramic compounds to efficiently perform the task needed. Each compound is doing a particular task in blocking, repelling or acting as a non-absorber to reduce the load and available transmission of heat.
J.E.’s Development Philosophy
J.E.’s stops long enough to think through what he could do to fix problems, then designs and redesigns formulas for the coatings to work properly. He concentrates on the challenge and not so much on making formulas initially. He takes a problem and finds chemistries to solve them. “The chemistry is already there, but you have to be willing to think and work completely outside the box (of accepted rules) to do trial and error failures until you start to see patterns develop toward a solution.” Each failure puts you closer to the solution as you see little things work and follow the small successes to the end solution. You cannot have a time limit, but you must run hard every day to find the solution because the “fix” is needed right now. That’s the reason learning the “don’t” of engineering and chemistry are kept behind a closed door.
Why you can’t get an “R” rating
In this process, it was uncovered that the current and very well established thought processes and systems for insulation materials are challenged. In the process of dealing with the misunderstood “R” rating and trying to compare this as a coating for explanation purposes, J.E. provided Super Therm® (the ambient heat block coating designed for repelling and blocking radiation heat gain) to the labs for Bombardier Engineering. Bombardier found Super Therm® could outperform other traditional materials that they had come to realise did not work inside the walls and ceilings of the passenger train cars being built at the time in Mexico City.
This type of ceramic coating technology is not required to have the standard “R” (resistance and conduction) ratings due to the fact that the heat never loaded to begin the calculation process. You must load heat “before” you can calculate R ratings which is simply the measurement of how much and how fast the heat is being absorbed and transferred through a material. If you do not load or at least reduce the load of heat, you do not have heat load and transfer and the R value is old technology and terminology.
Instead, Super Therm® is rated at 99% BTU block, meaning, it stops 99.5% of Infrared Heat and blocks radiant heat
The Heat Load
This is all to say that the “heat transfer” method of traditional materials is flawed in its’ concept and was never challenged when established back in the 70’s. It also allows for a 100% heat load onto the surface of the wall or roof. “Heat Transfer” then takes over to try and control how much and how fast this 100% heat load comes through and into the facility. What is heat load?
21st Century Heat Block
What the Super Therm® is designed to do for the 21st century solar heat block technology effort is to use the emissivity and reflective values of repelling and unloading heat loads. Emissivity is the ability of a surface to begin to load the heat and then throw it off at as high a percentage rate as possible. The reflectivity is the ability to block all three radiation waves (UV, Short Wave and Long Wave) from the sun and be specific about the ability to block these waves. The point of Super Therm® is to block the “loading” of surface heat during the heat of the day. You reduce the heat load, you reduce the heat transfer that is available to load into a wall or roof before it can transfer into a facility.
The most prime example of using the emissivity term wrongly is that concrete has an emissivity of .92. This is high, but is the concrete hot during the day and did it load and transfer through the wall? Yes. But at night, it can unload this surface heat quickly on the exterior. Even better example is the white car hood. White paint has a high emissivity to unload heat as explained by heat transfer methods. If this is so great, then sit on this hood during a 35°C day in good sun and tell me it is throwing off all the heat and not hot. This does not account for absorbing heat, it only accounts for throwing off heat when the radiation is blocked.
Stop heat load at the surface
Even when the K values are established and everyone knows it is performing better than the traditional materials, many will take the K value and try and fit it into the inch thickness formula and claim how this means that you must divide the Super Therm® K value by 1000 mils to see what the R value is per mil. K value is K value at whatever thickness is tested and stands as a fact of reality. To try and fit it into a thick material reality is throwing out the facts given by the test. In reality, we do not compare to the thick materials nor do we want to. Heat load and transfer is something that happens at the surface of the substrate. Traditional materials begin here, not after a full loading of heat and now only works to try and slow the transfer speed.
How Super Therm® is rated to block 96.1% of total solar heat
Engineers questioned J.E. on how Super Therm® is rated at a 96.1% heat block.
They said “You advertise you have a 95% heat reflectivity when the CRRC (ASTM testing for the ENERGY STAR) gives you only 84%”.
J.E. said that when doing the ASTM testing back in the beginning he was working with the lab and asked them if the test itself covered all the nano waves of the UV, Short and Long waves. He said no, the test was not designed to catch all the IR (long waves) in the initial set up because no one knew at the time that IR represented 54% of the heat.
I told them that is the reason SPI did testing originally with COSMO Oil in Japan to find a 99% reduction in IR and 92% reduction in Solar.
Then he did testing at the Academy of Science in Russia and Super Therm® blocked 96% of the total heat load.
Super Therm was then tested by the USA: Thermophysical Properties. Super Therm® blocked 99% of the BTU heat load from 367 down to just 3.99 BTU at 100°C. This equates to nearly 100% heat load block.
Then a US Energy Authority did testing and found Super Therm® blocked 99% of the heat load compared to a metal roof next to it. Uncoated roof loaded 164°F on a 85°F ambient day. Super Therm® roof loaded 86°F next to the uncoated roof while reducing the interior temperature by 10.2°F.
Bringing it down to 1°F over ambient is a 99% reduction.
J.E. said at that point, he simply averaged the test temperatures and gave a modest 95% reduction.
At this point, the engineers said it makes sense and they understood how SPI could make the claim.
Continued R&D
R&D is an ongoing process at SPI for the reasons that there are many other compounds not yet tested for effectiveness. Since research has been very limited in any laboratory sittings and this is a pure cost with no assurance of success, the research done and continuing at SPI will propel us into the future with a very high expectation of success and discovery.
Ceramics have come a long way from the high density form of making coffee cups to engines that can withstand high heat and resisting wear and tear to extremely light density ceramics that do not load heat and can repel heat loads. The understanding of this type of solution is on the upswing in the engineering communities and architectural fields and being adopted to reduce heat loads as the means to control heat gain or lost.
SPI solutions
SPI has worked on aerospace projects, heavy industry, oil and petrochemical plants to help with heat controls. Commercial and residential has been a focus of the uses over the past five years due to increased energy costs.
This technology applies to several products performing heat block for roofing and walls, with additional products developed for fire controls and to contain heat in pipes and boiler systems. As an example of the “insulation” that can be achieved with one of the water-based coatings applied directly over a 900°F-operating pipe, applying one inch of coating within a short time, the surface was reduced to 120F. The standard heat lost off the surface of the pipe was reduced and energy savings was ranging into 75% as calculated by standard engineering formulas.
J.E. has been a NACE member since 2001 and has advanced training courses. This cannot be achieved using standard traditional materials. In February 2008, J.E. was a speaker at the 12th Middle East Corrosion Conference in Bahrain on behalf of Saudi Aramco and was a speaker for NASA concerning the lead product called Super Therm® in Chicago in 1995.
He has developed encapsulation coatings Rust Grip® that are applied directly over rust to reduce prep, time and expense of sandblast with the use of a single coat system. Rust Grip® is patented for encapsulation directly over existing rust and directly over bio-hazard materials such as existing Lead-based paint and asbestos.
J.E. is a member of the “American Society of Naval Engineers”. SPI products have been certified under:
- Underwriters Laboratory
- Factory Mutual
- International Code Council
- US Coast Guard
- DET NORSKE VERITAS
- International Marine Organization
- China National Bureau for the Inspection of Technologies
- China Ship Building Corp,
- Japanese Institute of Standards
- Russian Certificate of Standards
- European Standards
Rust Grip – The Paradigm Corrosion Coating Shift
Rust Grip® was originally conceived and developed in 1988 by Joseph E. Pritchett, a renowned inventor of specialty industrial coatings. A new and different coating was needed to stop corrosion problems in the real world environment of the oil fields in Mexico and South America. Because of heat, humidity, and existing primitive methods of grit blasting, this coating had to have the following characteristics:
- Apply directly over surface rust;
- Apply as a one-coat system;
- Apply easily without extensive surface preparation;
- Penetrate through surface rust deep into the pores of the underlying substrate;
- Expand and swell into the pores and recesses to anchor and lock;
- Withstand abrasion and direct impact;
- Withstand acid rain and chemical splashes;
- Harden to a surface tensile strength for the petrochemical and heavy industrial areas;
- Withstand and protect from UV rays for use on the exterior of substrates;
- Possess durability and strength to last ten to twenty years in the harshest environments; and
- Use as a one part system – stir and apply.
In 1994, Joseph E. Pritchett and the company he founded, Superior Products International II, Inc., began the laboratory testing necessary to market Rust Grip® in the United States. During this testing process, the unique capabilities of Rust Grip® were revealed. The testing showed that Rust Grip® could be applied not only over surface rust, but also over existing paint with the ability to penetrate through the layers of existing paint deep into the pores of the substrate. This discovery led to the issuance of a process patent by the U.S. Patent Office on December 9, 1997, stating that Rust Grip® could be used as an encapsulant of lead-based paint, asbestos and other bio-hazardous materials. The patent (Patent #5,695,812) opened new markets for Rust Grip®, including bridges in the United States.
The capability of Rust Grip® to be applied over and to encapsulate lead-based painted surfaces or non-lead based painted surfaces has opened new avenues to protect and preserve existing bridges and other substrates at tremendous cost savings.