The Difference Between Rust Grip and Zinc Corrosion Coatings
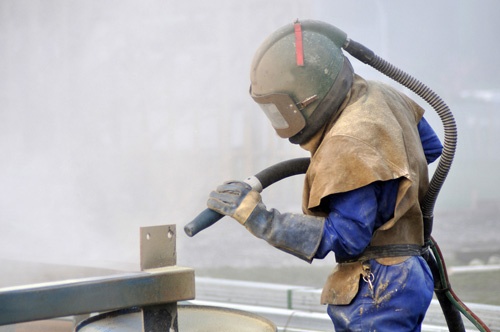
When it comes to zinc, they always specify a white blast to prep the surface to a clean white metal.
The reason for the white metal is because zinc cannot be applied over rust of any kind – even flash rust.
Reason is that zinc is self-scarifying, meaning it will give itself up to corrosion or being corroded or turning itself into rust to protect the surface under it. This is to offer a longer time before the rust actually begins to affect the metal surface.
The problem with all this “theory” is that the applicator must be standing ready as soon as the white metal blast is finished to begin applying the zinc primer. The zinc primer must be applied to white metal.
This is seldom if ever the situation. The blasting is finished and removes all this equipment. Then the painter shows up the following day or several days later to apply. Along coastlines, it takes hours for flash rust to develop or even interior in just days. It is called ‘blooming” of a light surface rust.
When the applicator applies the zinc on this bloomed surface rust, the zinc (being self-sacrificing) begins to allow itself to rust as it is designed to do.
The problem is that this is rusting directly on top of the metal surface which causes the metal to immediately begin to rust which eliminates the entire system of using a zinc primer, middle coat and top coat (3 part system).
From the beginning, this will fail within months or short years into the system life. Many times, it can be knocked off with a hammer in sheets due to the metal corrosion between the metal surface and the coating system on top.
Theoretically, the 3-part paint system should work for 20 years, but the white sandblast/then paint without flash rust, rarely happens and fails.
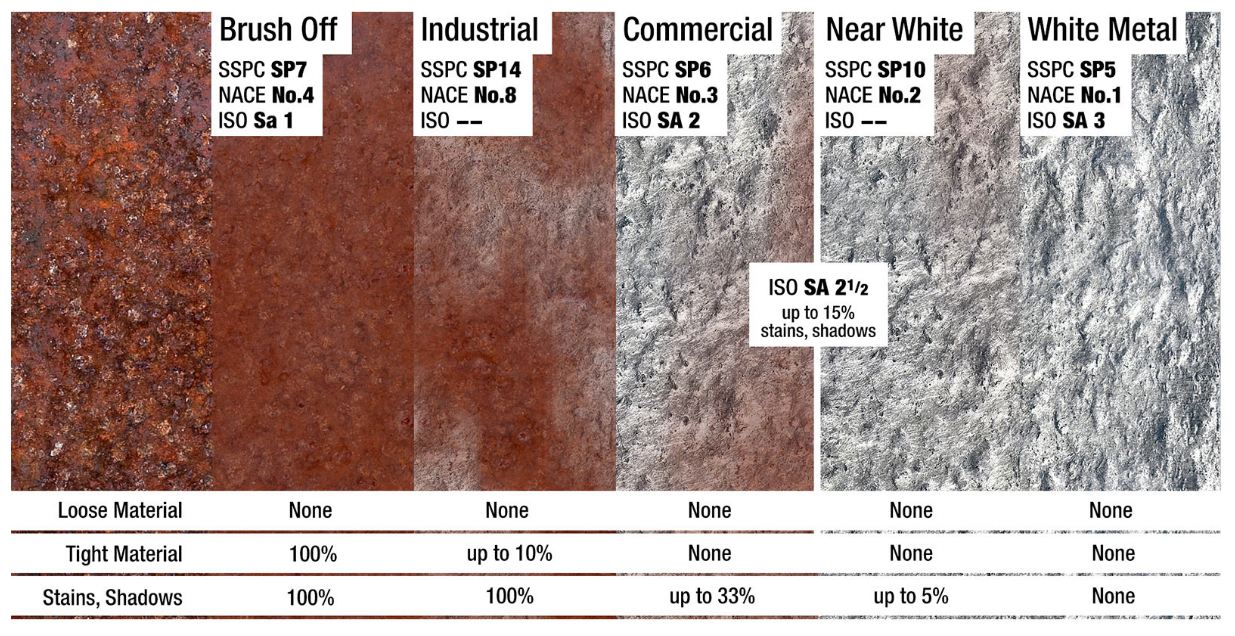
Traditional Zinc coating | Rust Grip® Aluminium coating | |
---|---|---|
Installation | • Requires lengthy sandblasting | • Minimal surface preparation |
Application | • Involves multiple coats Epoxy • 3 Coat Systems • 4 Coat Systems |
• Polyurethane moisture-cure metallic, that cures faster. The higher the humidity the faster the curing • Total application time maybe reduced by 75% |
Moisture Prevention | • Limited protection from mould and mildew | • Stops water vapor transmission through electro-chemical freezing |
Longevity | • Shorter lifetime endurance | • Penetrates deep into pores of surfaces |
Corrosion | • Not effective at blocking long-term degradation | • Adds strength to weakened surfaces |
Repair and Maintenance | • Requires continual repair or complete overhaul | • Reduced surface preparation and efficient application yields cost savings |
Surface Preparation | • Sand Blasting • Sa 2.5, NACE2, SSPC10 |
• Cost is reduced due to high surface tolerance of Rust Grip® • SSPC1+SSPC2+SSPC3, St.2+St.3 • Grit/Garnet cost eliminated or reduced by up to 75% |
Encapsulation | • Unable to encapsulate | • Encapsulation of Asbestos, Lead-based paint and Biohazards |
Configuration | • Multi-component system with various mixing ratios |
• Self priming • Single-component system consists of only Rust Grip® |
Performance | • Limited Performance • Cannot match Rust Grip®‘s Laboratory or field performance | Perfect Score: • ASTM B117 Salt Spray Fog Test: 15,000 hours = 30 years • ASTM D5894 Standard Practice for Cyclic Salt Fog/UV Exposure of Painted Metal; 10,000 hours • ASTM E1795 Standard Specification for Non-Reinforced Liquid Coating Encapsulation Products for Leaded Paint in Buildings |
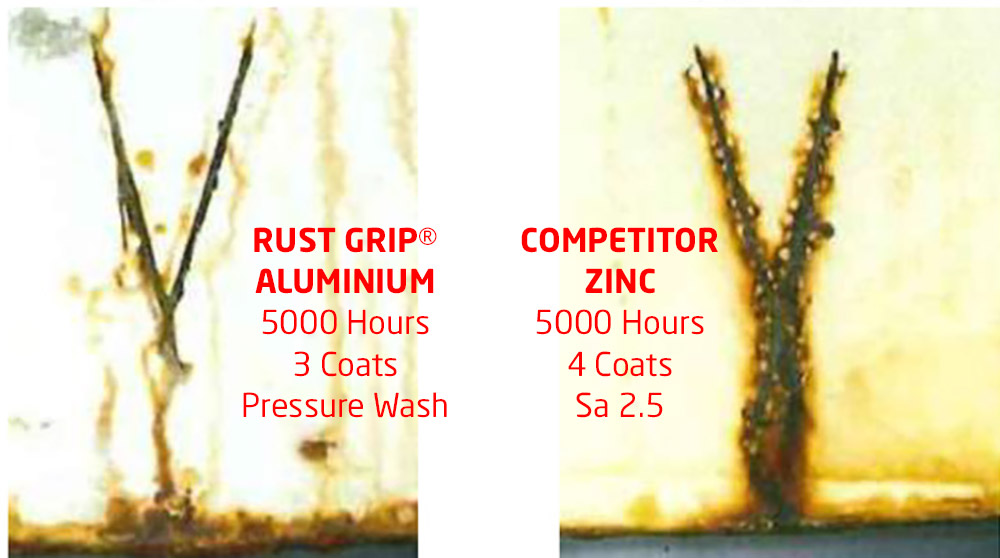
Traditional concept of corrosion control
All corrosion coatings in the market are TOPICAL coatings – do not penetrate the surface
TOPICAL coatings adhere to roughness on the surface layers like a GLUE and are susceptible to attrition and loss of adhesion over time
Oxidation and acid rain can enter and set off corrosion even though the surface coating remains intact
Surface developed flash rust before coating was finally applied – coating was not designed to penetrate and encapsulate
Topical coatings allow corrosion to develop inside pores – corrosion develops in six (6) months to two (2) years
Traditional bridge coating systems (TOPICAL coatings) perform optimally at SSPC-SP10 (Near-White Metal Blast Cleaning) surface preparation – requires abrasive blasting to abate the substrate and prepare surface
Dangers of abrasive blasting and other blast media practices are well documented
Serious adverse environmental impact – air, water and soil contamination, worker exposure, pollution and noise
Near-white metal blast produces a minimum of six (6) and up to eight (8) pounds per square foot of spent abrasive
Four 1,219,200 m2 of paintable surface can generate anywhere from 13,000 to 21,000 tons of spent abrasive
What if there’s a Zinc coatings can’t be removed?
If a project or site cannot be blasted or you can’t pressure clean or treat the area. Firstly thoroughly clean the surface, remove all dust, flaking etc.
Firstly, Zincs and Urethanes DON’T MIX so it needs an Epoxy coating between them. You cannot use Rust Grip directly over any Zinc coating because it’s a urethane.
Our Epoxy corrosion coating Moist Metal Grip can be hard brushed into surface, around the bolts and everything at 100 microns.
This will not fix the current corrosion but it should stop future growth. Then you can apply Rust Grip (urethane) or Enamo Grip (epoxy) on top of the Moist Metal Grip (epoxy).