Corrosion Control for Transmission Towers
The following pictures in the Panama mountains show the electrical transmission lines and metal towers. The rusting and deterioration was stopped by Rust Grip®. In the humid jungle areas with condensation or constant rain, Moist Metal Grip was used with an overcoat of Enamo Grip S/B. Utilities companies are under constant challenges with corrosion…both atmospheric but also underground with the buried pilons to keep the energy grid operational.
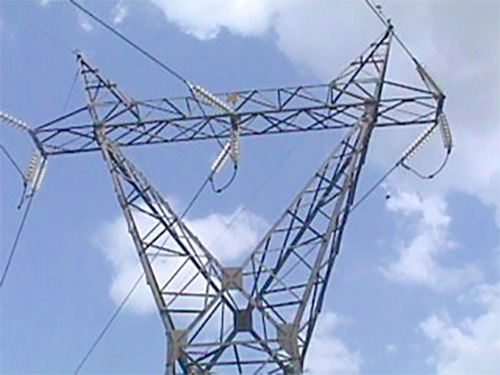
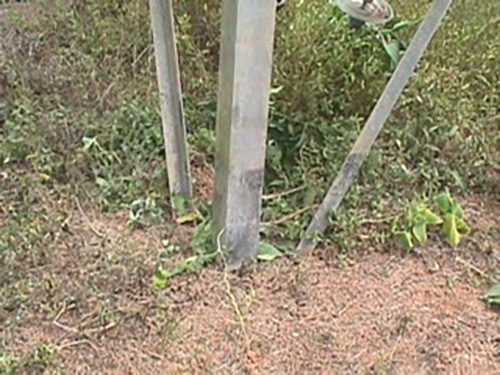
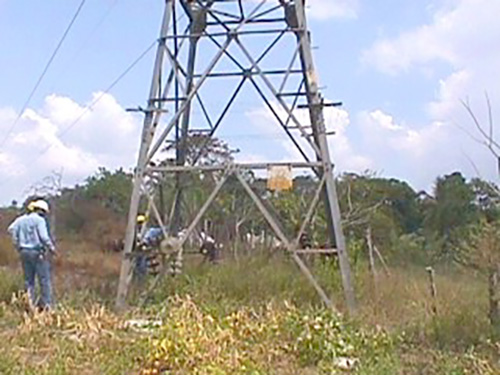
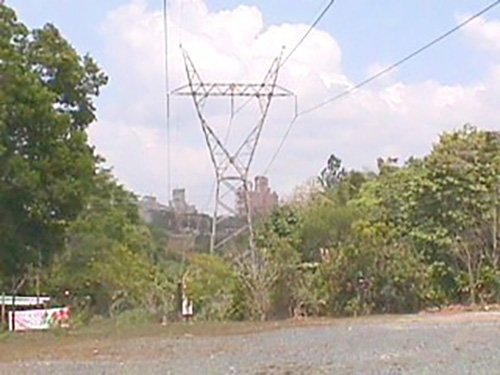
The electric power utility industry commonly uses galvanized steel for power transmission poles, lattice towers, and other transmission and distribution assets—particularly high-voltage transmission line structures and substation structures—because it is known to be well-suited for service in most atmospheric and underground environments and has a long record of proven performance. According to the American Iron and Steel Institute, close to 1 million steel distribution poles have been installed in the United States since 1998 and are being used by more than 600 U.S. electric utilities. (source)
Galvanized structures typically exhibit a low corrosion rate because a continuous passive film, known as a zinc patina, forms on the pure zinc top layer of the galvanized surface when it is exposed to the atmosphere. Since zinc is anodic to steel, the hot-dip galvanizing also acts as a sacrificial anode if the galvanized coating is physically damaged to some degree. If individual areas of underlying steel become exposed, the surrounding zinc will provide sacrificial cathodic protection (CP) to the unprotected sites by corroding preferentially. The zinc is consumed as it sacrifices itself to protect the bare steel.
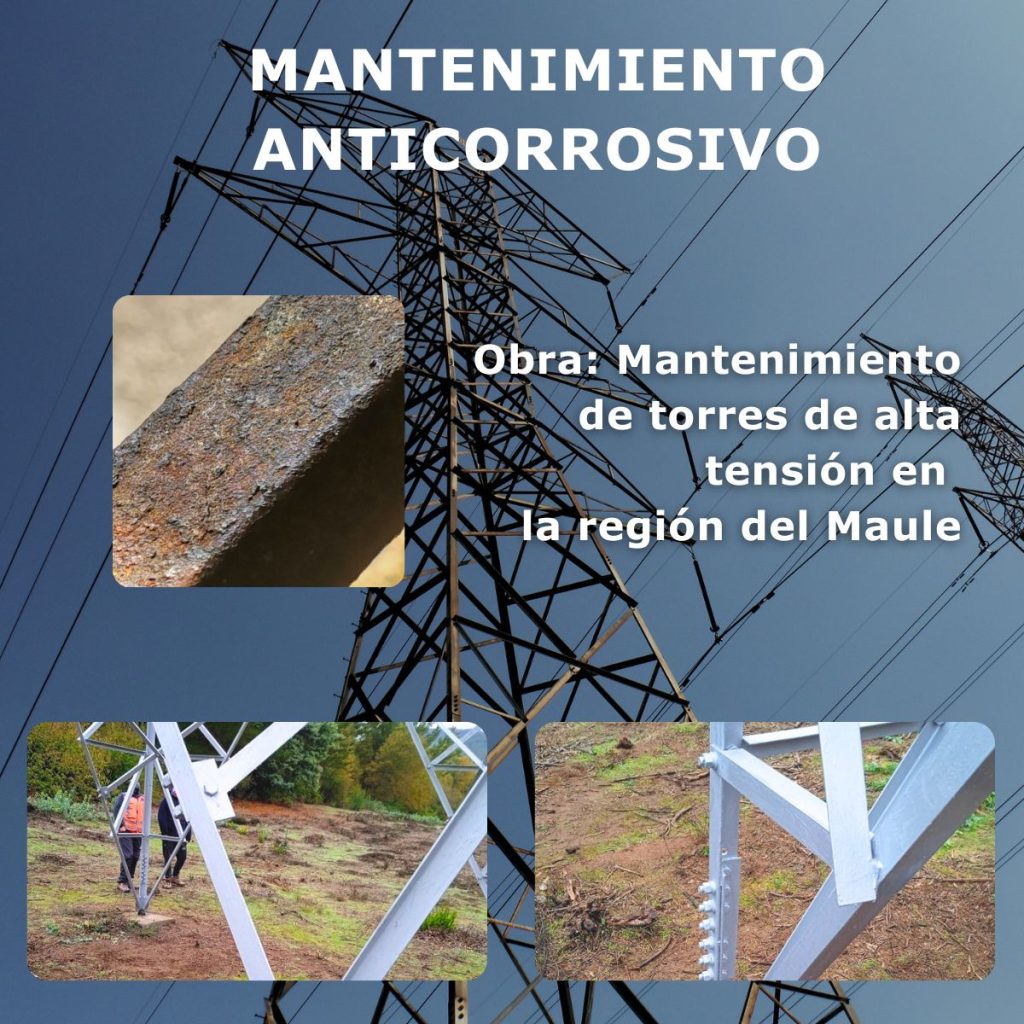
Why Rust Grip is the solution?
Rated No 1: Rust Grip® is a high performance, tough, aluminium based easy, moisture cured polyurethane encapsulation coating; corrosion, lead paint, asbestos and bio-hazards.
ALL successfully passed (ISO 12944-6 C5H) atmospheric corrosion testing. As you may know this is one of the toughest tests around. Charter Coating Laboratories is an ISO 17025 accredited lab which means their results can be used worldwide. ISO 12944-6 test is for all onshore and coastline atmospheric corrosion protection. As a testament to our performance, we did not have a single pull off below 1,000 psi and regularly pulled over 2,000 psi with a max pull of 2,505 psi. No blistering, rusting, or flaking were observed on any panels. We also always maintained a required average minimum scribe creep at less than 3mm.
Systems Tested:
- Rust Grip® @ 200 micron DFT
- Rust Grip + Enamo Grip @ 300 micron DFT
- Rust Grip + Moist Metal Grip + Enamo Grip @ 400 micron DFT
The last attachment is Petrobras Oil group (Brazil) that performed the same test in their “off-shore” rig following the same ISO 12944-6 except off-shore version.
This covers:
This ISO 12944-6 is the latest testing being required by engineering worldwide.
Rust Grip rated #1 by the Society of Petroleum Engineers
A long-term lab and field study by Chevron published by the Society of Petroleum Engineers, tested 18 different coatings on drill pipes for eight years. Drill pipes are the toughest environment anyone can ever imagine and Rust Grip® was the top performer. In that paper they highlight the cascading benefits that came from solving the corrosion problem. You solve the corrosion problem, that’s already millions of dollars in savings and then because you’re not having to swap out these drill pipes so often, you’re saving millions in logistics.
You’re not dealing with the worry of a corrosion issue, the toughness of Rust Grip® is outstanding!
Here’s and interesting video presented by J.E. Pritchett, the inventor and President who has 35 years of coatings research > Corrosion Encapsulation with Rust Grip Explained
See more about Rust Grip® video | Rust Grip Brochure
Rust Grip Benefits include:
- Single Component – No mixing part A & B
- Fast Cure – Humidity accelerates curing
- Surface Tolerant – Minimal surface preparation
- Self Priming – “Three coats in one” system
- Strength – Non leafing aluminum metallics
- Easy to Apply – Brush, Spray or Roll
- Summer – Apply on surfaces up to 60C
- Long Shelf Life – 3 years if unopened
No Air, no Moisture = no Corrosion!
Rust Grip® – The Paradigm Shift Corrosion Coating
Our Competitors
Rust Grip is used on some of the largest projects and LNG carriers in the world and has proven in lab testing against leading competitors.
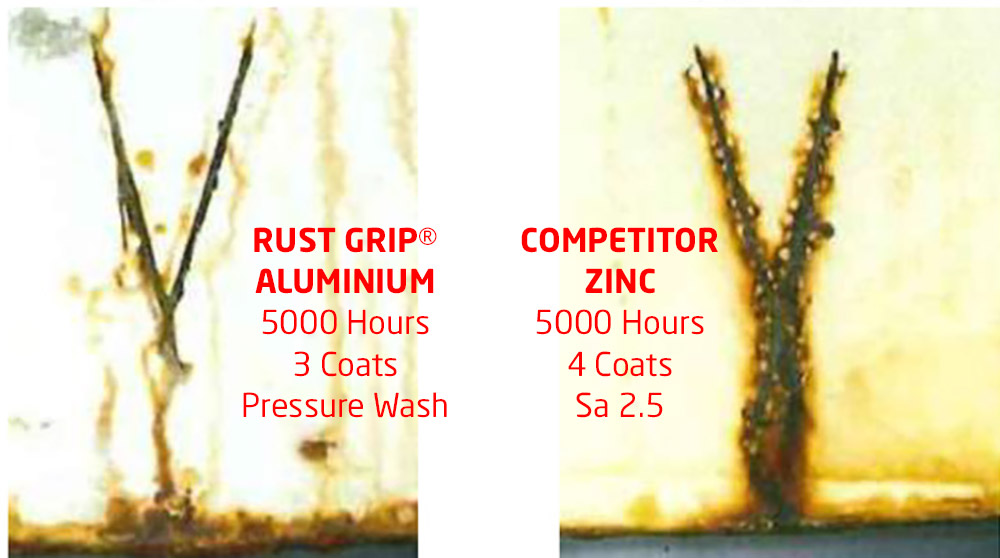
In the test attached, Rust Grip was only power washed (4000 psi) with 3 coats applied to DFT of 300 microns for this test whereas the competitor three coat zinc epoxy urethane system was both pressure washed and blasted yet could not match Rust Grip’s corrosion protection. I would recommend 3 coats of Rust Grip due to the tough environment and one coat of Enamo Grip white/clear as Rust Grip is only available in silver colour due to the aluminium pigments.
Surface Preparation
Brush applications certainly create the strongest pull test results for Rust Grip as it really gets into the pores of the substrate.
The key to Rust Grip is ensuring the base surface is 100% dry. A wet or moist surface will compromise Rust Grips ability to bond and encapsulate the surface. We have a time/humidity chart attached for Rust Grip which shows how you can paint three coats in a single day if you have over 40% humidity.
Minimum preparation: Hand tools, either mechanical wire brush or hand wire brush. If in salty environment we recommend Chlor Rid as part of the power wash. Use citris dishwashing liquid to clean surfaces.
Optimum preparation: NACE 4 brush off blast.
Pack or Mill scale rust: NACE 3 commercial blast – 95% of the times you’ll only need a NACE 4 if you choose to blast.
Applicator Safety: If it’s applied on external surface only the applicator needs to wear a respirator for applying solvent based paint. VOC compliance maybe necessary as Rust Grip is 347 grams per litre. If painting Rust Grip inside for example like ballast tanks then you would need very strong ventilation with two or more openings and full face mask.
Essentially: Imagine: 3 days work in a single day, at half the price and double the corrosion performance! Think it’s too good to be true…you can’t afford not to use Rust Grip®!
Some Questions
Can Rust Grip go over zinc coating?
Rust Grip can’t be applied over zinc rich coatings however it should be fine on galvanized zinc coating. Best to test some areas.
Can Moist Metal Grip go over concrete?
Moist Metal Grip is our subversive, pooled water 2 part corrosion coating and is excellent on concrete. Will be perfect at the base of a tower near water. If the concrete is porous, put on first coat blend with MEK or acetone 20% to thin it out. It will penetrate in further and lock out. Then full strength coat on top. MMG is easy as you have 72 hours to recoat unlike Rust Grip. But as soon as the coat is dry to the touch you can apply the next coat. It’s chemical curing but dry to touch will mean it’s done gassing.
What is the surface profile to apply Rust Grip?
There’s no surface profile required but we want 100 microns over the peak profile. So if there’s a 50 micron deep profile then we want 150 microns total. If you’re specified to blast go 25 microns, just a light sweep.
Dew point
Data sheets say 2.5°C. However as long as the moisture is not getting on the coating you can apply, ie you have protection like a tent. Moisture in the air will accelerate it.
How to know when Rust Grip is ready?
Follow the temp/RH chart. Essentially the coating is not tacky but you can dig your nail into it with slight resistance.
Spread rate is up to 50m2 per 5 gallon / 18.9 litre pail (2.5m2 – 3.3m2 per litre) is $22.68m2 depending on the level of rust / corrosion that it needs to penetrate.
Some Companies using Rust Grip® Globally
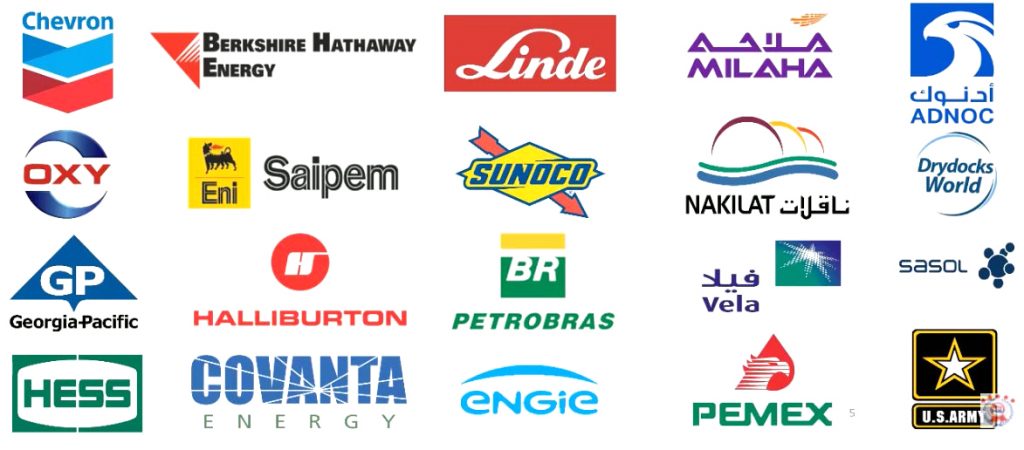