HPC® Coating FAQ
General HPC® Coating Questions
What is HPC® Coating?
HPC® Coating is a high-performance insulation and corrosion protection coating designed for industrial applications. It functions as a closed-cell insulation that blocks heat loss and prevents corrosion under insulation (CUI). HPC® Coating (Hot Pipe Coating) is a ceramic based, water-borne insulating coating designed to insulate in high temperature situations from ambient to 650°C. Use HPC® Coating as an insulation to block heat loss, save energy, reduce maintenance, stop CUI (Corrosion Under Insulation), reduce landfill and personnel protection.
What temperatures does HPC Coating operate in?
HPC® Standard – Ambient up to 204°C
HPC® Coating is water-borne and extremely lightweight in appearance. It uses a special acrylic resin blend with specific ceramic compounds added to provide a non-conductive block against heat transfer.
HPC®-INT – 204°C up to 426°C
HPC®–INT Coating is designed to control heat transfer on surface. It’s water-borne and extremely lightweight in appearance. HPC®–INT Coating uses a special acrylic/silicone resin blend with specific ceramic compounds added to provide a nonconductive block against heat transfer.
HPC®-HT – 426°C up to 650°C
HPC®–HT Coating is a two-part hybrid silicone/solvent resin (Part A and B is a water-based resin system) using specific ceramic compound loads for application directly over surface temps of 426°C (800°F) and up to 650°C (1200°F). It is designed to block and hold the interior temperature on the surface and reduce conductive heat transfer loss.
How does HPC® Coating work?
HPC® Coating creates a hermetically sealed surface using 7 original ceramics and tough resin coating system, preventing air and moisture penetration to the surface and reducing heat loss off the surface. This reduces heat transfer and eliminates two key catalysts (moisture and air) for corrosion under insulation (CUI). The ability of a coating to block heat load is crucial for its success and results. Read the pdf below to understand why HPC Coating differentiates and performs the best!
What are the main benefits of using HPC Coating?
- Blocks heat loss and improves energy efficiency
- Eliminates corrosion by sealing out air and moisture (CUI)
- Replaces wraps and jacketing traditional insulation materials
- Long term energy savings
- Money savings
- Reduces long-term maintenance costs
- Carbon emissions reductions
- Personnel protection below 50°C
- Easy to repair and easy to maintain
- Water based and safe application
- No shut down required
- Long lasting and durable
Applicability of HPC® Coating
HPC® Coating is widely used for industrial pipelines, tanks, and infrastructure requiring insulation and corrosion protection. It is ideal for applications where heat loss needs to be controlled and corrosion under insulation (CUI) is a concern.
Common use cases include oil and gas pipelines, storage tanks, and industrial processing equipment. While HPC® Coating is effective in many scenarios, surface preparation is crucial, and an additional topcoat like Super Therm may be needed for external applications.
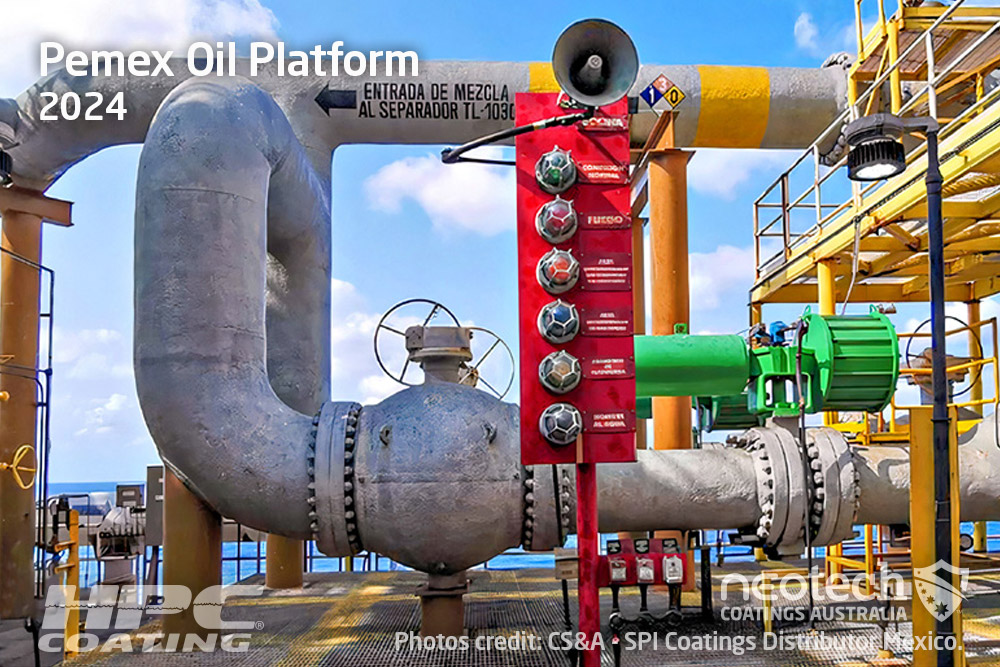
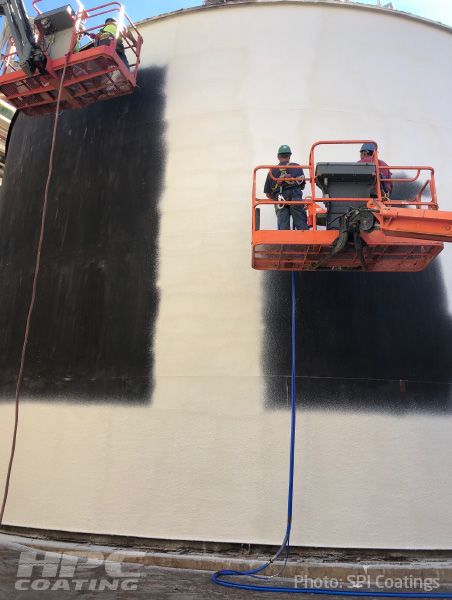
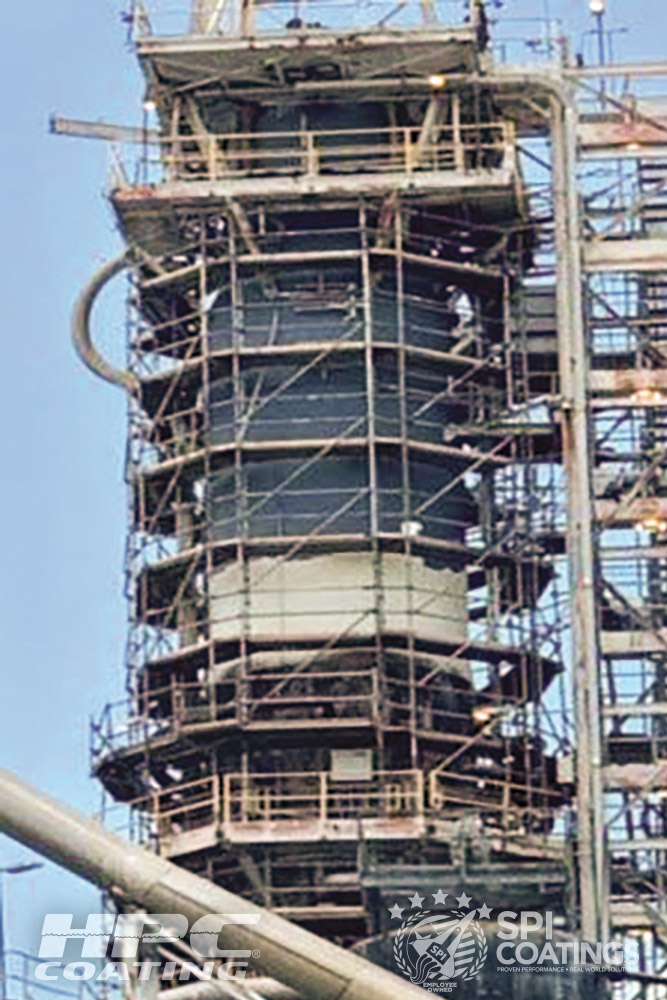
Corrosion Protection
Does HPC® Coating prevent corrosion?
Yes. HPC® Coating forms a sealed barrier that prevents air and moisture infiltration, reducing the risk of corrosion under insulation (CUI). This was demonstrated in a project with Georgia Pacific, where corrosion did not expand despite existing rust beneath the coating.
Is a topcoat necessary for external applications?
For external applications, it is recommended to apply Super Therm as a topcoat over HPC® Coating to enhance protection and stabilize the surface further.
Application & Installation
How is HPC® Coating® applied?
HPC® Coating can be applied via spray, brush, or roller, depending on the surface and project requirements. Surface preparation includes cleaning and, if necessary, using Rust Grip as a primer.
How many coats are required to achieve the desired thickness?
The number of coats depends on the required dry film thickness (DFT). This is determined by project specifications and should be confirmed with an SPI engineer.
What is the recommended surface preparation before application?
- Ensure the surface is clean and dry.
- If there is existing corrosion, Rust Grip can be applied as a primer ideally.
- If the surface is too smooth, it may require abrading for better adhesion.
What are the recommended application conditions?
Ideally the warmer the better for HPC® Coating application. It is a waterbased product so takes time to dry and cure. Steam pipes in situ running at higher temperatures will cure down quicker than ambient surfaces. For ambient environments we recommend warmer months for application.
Weight per m2
The weight per metre of coated pipelines depends on the coating thickness. As HPC® Coating is a ceramic-based insulation, it adds minimal weight compared to traditional insulation methods. If you provide the pipeline dimensions and required DFT, we can calculate the exact weight impact for your structural and logistical planning.
Cost & Return on Investment
How much does HPC® Coating cost?
HPC® Coating (rated for up to 200°C) is priced at $755+GST AUD per 5 US gallon (18.9 litres) pail (as of 1st February 2025).
How do I calculate how much HPC® Coating I need?
The spread rate depends on the thickness required. For 2540 microns DFT:
- Spread rate = 5.5 m² per pail
- 500 m² roof surface area: Approx. 90 pails
What is the typical return on investment (ROI) for HPC® Coating?
ROI depends on energy savings. In a Georgia Pacific project, HPC® Coating provided a return within 13 months based on GP engineering data.
Thermal Performance & Standards
What is the thermal performance of HPC® Coating?
HPC® Coating is tested under:
- ASTM C177 for thermal conductivity
Conduction Testing via ASTM C-177 Method:
Thermal conductivity over three tests: 0.560 BTU
To find the Lambda Value or K (0.560 X 0.144 = 0.0806 k value – Average 600 mils (14mm)
Convert k 0.0806 X 0.5778 (Heat Conversion Handbook Pg. 506) to K for sq.m = 0.0466.
Whereas R = 1/K = 21.46 - ASTM Flash Method (E 1289 and E 1461-92)
Conduction Testing via the ASTM FLASH METHOD (E 1269 and E 1461-92)
K value average is 0.1083
0.1083 X 0.5778 = 0.063K for sq.m
R-1/K – 15.87
Average 38 mils (.90 mm)
A detailed thermal analysis (energy efficiency vs. DFT) can be provided upon request or see this report.
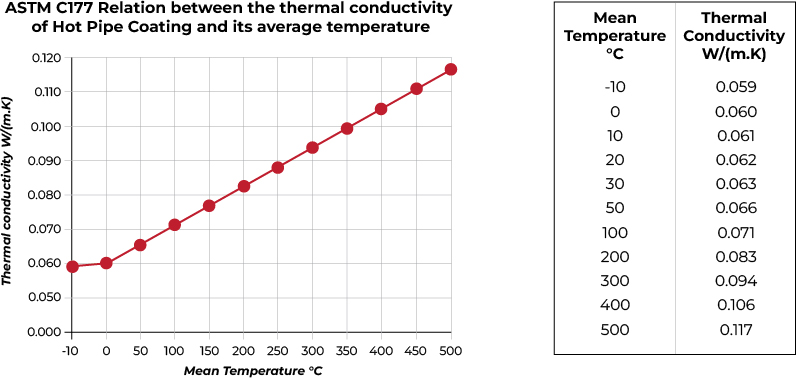
Does HPC® Coating meet Australian Standards?
HPC® Coating is part of advancements in materials science, addressing modern insulation challenges. While these coatings represent new technology, they are being tested and specified by leading Australian companies such as Viva Energy and FirstGas NZ but not yet regulated. CSIRO is testing Super Therm® for a thermal insulation coating standard which will be a first in Australia, meanwhile thicker insulation coatings are not regulated or rated.
Case Studies & References
Are there any case studies for HPC® Coating?
Yes, case studies include:
- Georgia Pacific (EPA Award-winning project)
- Pemex Oil Gulf of Mexico
- Various field studies demonstrating effectiveness in reducing heat loss and preventing corrosion
Who has specified HPC® Coating in Australia?
Viva Energy has already specified HPC® Coating for use on-site.
Safety Data Sheets (SDS)
Safety Data Sheets (SDS) for HPC Coating are available here.
- HPC® Standard – Ambient up to 204°C – pdf (Australian HPC SDS pdf)
- HPC®-INT – 204°C up to 426°C – pdf
- HPC®-HT – 426°C up to 650°C – pdf
These documents provide essential compliance and safety information regarding the coating’s composition, handling procedures, and potential hazards.
Ordering & Payment Terms
What are the payment terms for purchasing HPC® Coating?
NEOtech Coatings Australia are the exclusive Distributor for Australia, New Zealand and the South Pacific. Regrettably we do not offer credit. Standard payment terms apply depending on availability and supply needs:
- 70% upfront payment upon order
- 30% payment upon landing in Australia
All other global enquires please visit the owners and manufacturers SPI Coatings today!