Super Therm Japan Industry Case Studies
Nissan, Japan: Super Therm® Energy Reduction Coating
Good-Standing Factories in Energy Control
Improvement Case Examples – Japan
Factories that were awarded by the Secretary of State for Trade and Industry-Director and General of the Agency of Natural Resources and Energy.
(1998 Electric Category : 19 Case Examples)
April, 1999
National Electricity Saving Committee
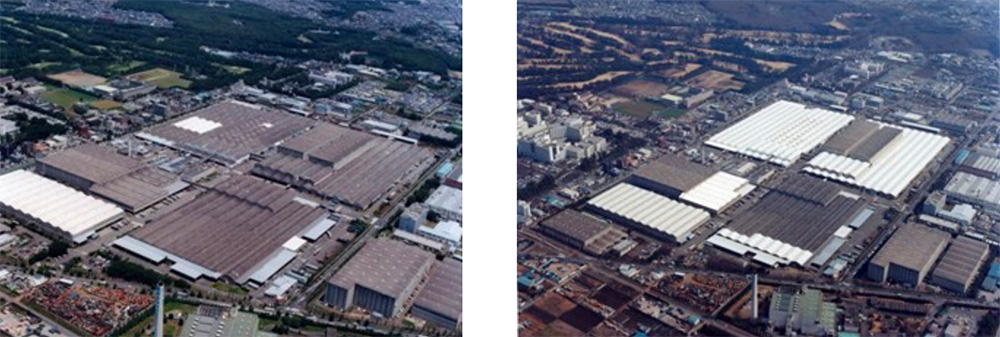
Good-Standing Factories in Energy Control in 1998
Electric Category: List of Awarded Factories
(1) Secretary of State for Trade and Industry-Director (5 Cases)
Area | Company | Industry |
---|---|---|
Tohoku District | Tohoku NEC Corporation | Manufacturer of Electric Machinery and Equipment |
Chubu District | Sony Koda Corporation | Manufacturer of Electric Machinery and Equipment |
Kinki District | Osaka Gas Co., Ltd. | Gas Provider |
Chugoku District | Seibu Oil Co., Ltd Yamaguchi Oil Factory | Manufacturer of Petroleum and Coal Products |
Kyushu District | Miyazaki Tourist Hotel | Accommodation |
(2) General of the Agency of Natural Resources and Energy (14 Cases)
Area | Company | Industry |
---|---|---|
Tohoku District | Tohoku Paper Industry Co., Ltd | Manufacturer of Paper and Paper Products |
Tohoku District | Miyagi Oki Electric Industry Co., Ltd | Manufacturer of Electric Machinery and Equipment |
Kanto District | Ricoh Co., Ltd Gotenba Branch | Manufacturer of general Machinery and Equipment |
Kanto District | Asahi Glass Co., Ltd. Sagami Branch | Manufacturer of Glass Products |
Kanto District | Torii Pharmaceutical Co., Ltd. | Sakura Factory Chemical Industry |
Kanto District | Topcon Corporation | Manufacturer of Precision Machinery and Equipment |
Chubu District | Melco Inc. Kakegawa Factory | Manufacturer of Electric Machinery and Equipment |
Chubu District | Showa Gousei Co., Ltd. | Manufacturer of Transport Machinery and Equipment |
Chubu District | Denso Corporation Nishio Factory | Manufacturer of Transport Machinery and Equipment |
Hokuriku District | BFU Co., Ltd. | Manufacturer of Electric Machinery and Equipment |
Chugoku District | Kanebo Ltd. Boufu Factory | Chemical Industry |
Chugoku District | Japan Tobacco Inc. Yonego Factory. | Tobacco Manufacturer |
Shikoku District | Teijin Ltd. Matsuyama Branch | Chemical Industry |
Kyushu District | Bank of Saga Ltd. | Banking and Trust |
Application of Insulation Coating on Factory Roofs
Factory Information
Capital | ¥2000 Million ($17 Million) |
Contract Demand | 4,700kW |
Voltage | 33kV |
Site Area | 181,751 sqm |
Building Area | 86,000 sqm |
Main Product | Video Camera |
Electric Power Consumption Rate | 1,320,000kwh/ ¥1million |
% of Electricity Cost in Production Price | 0.18% |
Workers | 2,500 |
Electricity Related Workers | 7 |
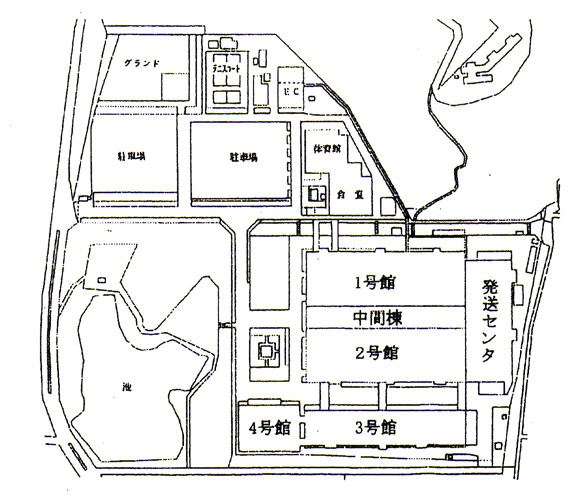
Building Name | Area (sqm) | Note |
---|---|---|
Building 1 | 12,600 | |
Building 2 | 12,600 | |
Building 3 | 7,100 | Not applied |
Building 4 | Not included | |
Middle Building | 4,400 | |
Shipping Centre | 6,900 | |
Dining Building | 2,400 | |
Gym | 1,600 | Not applied |
Energy Centre | 1,400 | |
Total | 49,000 |
Reasons for improvement
Out of all electric energy that this factory consumes, the energy used for air conditioning is high, and it takes up about 30%. The energy consumption rate for air-conditioning in summer is especially increasing due to the automation of offices and factories.
There are nine buildings in this factory and the first construction of Building 1 began in 1973, and the construction of the roofs was corrugated metal sheets + paint. Due to this roof construction, it had poor insulation performance, and it was a burden to the air conditioners in summer.
The temperature of the roof surface was very high due to the radiant heat, and the work environment was also poor. They had to lower the temperature setting of the air conditioner. Therefore, there was a need for improvement in energy saving.
Improvements
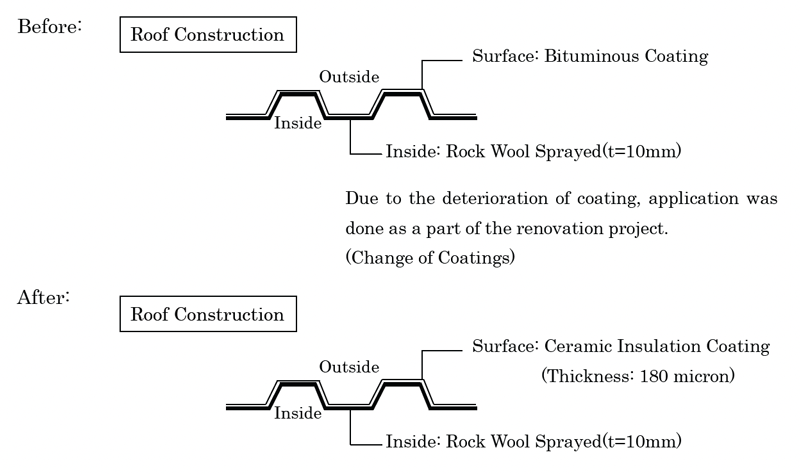
Ceramic Insulation Coating was applied by spray in two layers to the surface of corrugated metal sheet roof.
Composition: COOL THERM = Super Therm® in Japan
Water-Base Paint (Acrylic Resin + Urethane Resin + Four Kinds of Ceramics)
Results
Energy Saving
Condition: Fine day in summer Outside Temperature: 32C (90F)
Outside Surface Temperature | Room Surface Temperature | |
Before | 63C (145F) | 61C (141F) |
After | 41C (105F) | 38C (100F) |
Difference | ▲22C (40F) | ▲23C (41F) |
Energy Saving Effect:
40,300sqm × 23C (73F) × 2.76Kcal/h⋅sqm⋅C
(K Value: over-all coefficient of heat transfer for steel)
= 2,558,244kcal/h
2,558,244kcal/h × 8h/day × 20 days/month (Period of Air-conditioning Used) × 6 months/year (Fine Sky Ratio) × 0.75
= 1,841,760 Mcal/year
Calculation of Electricity:
1,841,760 × 103kcal/year ≑ 3,000kcal/h⋅RT × 1.2kW/RT
= 736,704kWh/year
Energy Saving Cost:
736,704kWh/year × ¥15/kWh = ¥11,050,560/year
Prolongation of Life Span
The re-painting cycle has extended from seven years to nine years.
Improvement Evaluation
Initial Cost for Improvement (¥10,000) (A) | Energy Saving Effect (¥10,000/year) (B) | Pay-Back Period (year) Excluding Interest (A/B) |
Ceramic Insulation Coating: 6,850 | ||
Bituminous Coating: 5,680 | ||
Difference: 1,170 | 1,105 | 1.06 |
Return on Investment
Thirteen (13) month payback savings to investment over the difference in cost of applying Bituminous Coating which has no insulation payback.
Comparison of cost
Bituminous versus Super Therm®. Super Therm® is 20% more in cost but returns its total investment in 13 months compared to 0 return from Bituminous basing on the difference in cost of both systems.
Super Therm® alone has a 6.16 year ROI.
Sony Koda reduced 75% energy consumption with Super Therm®
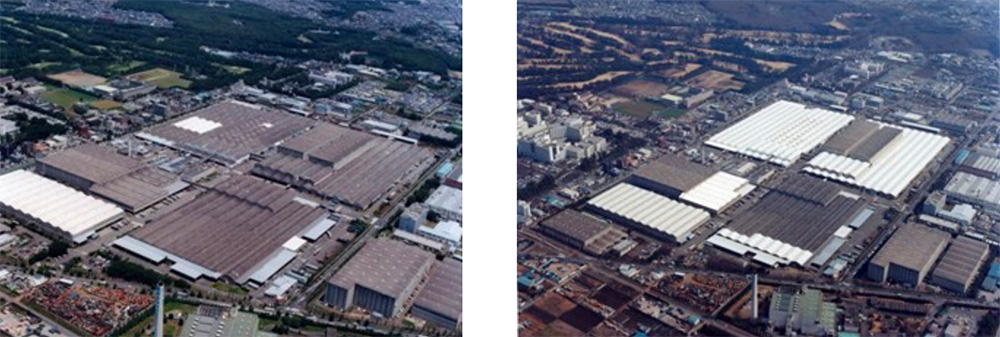
Above Nissan Factory, Yokahama, Japan: 200,000m2
Sony Koda Application | May | June |
Before Super Therm® applied | 3,767 KW | 5,647 KW |
After Super Therm® applied | 519 KW | 1,896 KW |
TOTAL KW REDUCTION | 87% | 67% |
Source: Daiko Shokai, Japan | See more Japanese Saving Case results (pdf)