Thermal Insulation Coatings
Thermal insulation and Thermal insulative coatings are liquid based and cure to simultaneously form a protective finish and provide resistance to heat flow. They are based on advanced materials and unique formulations applied to surfaces operating at elevated temperatures. While thermal insulation coatings can be used in negative temperature environments, they are best suited for warm to hot assets.
The thermal insulation coatings from SPI the manufacturers are world innovators based on specific ceramics and can range from 250 μm (microns – 0.25mm) to 30 mm thick that serve to insulate components from large and prolonged heat loads and can sustain an appreciable temperature difference between the load-bearing metals and the coating surface.
There is a difference however between thin and thick thermal insulation coatings that have multiple ceramics. Unlike many competitors that develop acrylic coatings that rely on low conductivity fillers such as aerogel or silica based gels our coatings are ceramic based. Thin coatings block the heat and push it back to the source such as radiation heat from the sun. Thick coatings are design to contain and hold as much heat as possible such as steam pipes and boilers. In doing so, these coatings can allow for higher operating temperatures while limiting the thermal exposure of structural components, extending part life by reducing corrosion and thermal fatigue.
In conjunction with film heat management, thermal coatings permit working fluid temperatures higher. Due to increasing demand for more efficient pipes at higher temperatures with better durability/lifetime and thinner coatings to reduce operation costs there is significant motivation to develop new and advanced thermal coatings. The material requirements of thermal coatings are similar to those of heat shields, although in the latter application emissivity tends to be of greater importance.
Access to energy is an important global driver for economic growth, and how we generate, efficiently use, and ultimately conserve energy has important consequences for the future of our environment and society. Coatings technology has an important role to play in this ongoing struggle. For example, coatings that can be cured at lower temperatures inherently use energy more efficiently (source).
Several types of functional coatings are targeted at managing thermal energy. Cool-roof coatings keep the interior of buildings cooler and lighten the load on air conditioning during the hot, sunny days of summer. High solar reflectivity and thermal emissivity helps the coating deflect energy in sunlight, preventing the roof from heating up as much, and thus less heat is conducted through the roof and into the building. Cool coatings for exterior building walls also function in a similar manner.
Cool coatings also help defend against the urban heat island effect, where urban environments with large areas of dark roofs and paved surfaces tend to be warmer than nearby rural areas. Thermal insulation coatings are also used to manage thermal energy for both personnel protection and energy conservation purposes. However, thermal insulation coatings rely on a different mechanism and prevent heat transfer between materials due to their low thermal conductivity.
In this article, we introduce thermal insulation coatings and the science behind how they work. First, a discussion on the physics of heat transfer and thermal conduction will provide some necessary context to understand how insulation works. A description of traditional insulation materials and some lingering problems with those materials will give perspective into why thermal insulation coatings were developed, followed by a description of how thermal insulation coatings are formulated, applied and perform. A brief comparison with cool-roof coatings will also be given to clarify common misunderstandings about functional coatings and how they each help with energy management.
Spray-on Ceramic Insulation up to 450°C and Encapsulating existing corrosion without sandblast
Joseph E. Pritchett, (AM)
Superior Products International II, Inc., Research Center, USA
Abstract
Ceramic compounds have been around for many years, but the research to find which compounds, what size, crystalline structure and density would perform to block “heat load” is the keys the selecting the correct compounds to use. “Blocking heat load from radiation or resisting the absorption and loading of heat when used over a hot surface” is determined by the aspects stated above. None of this could be determined from the ceramic catalogs of listed compounds stating referenced characteristics. To determine how a compound would react in a paint/coating form could only be realized by trial and error when the compound is mixed in a resin solution with other compounds to see the result. This process has taken 33 years and over 4000 compounds to find 12 compounds that will continue to work when wet and mixed with other materials.
Driving Force
As a direct response to the international business community’s acknowledgement of the benefits of insulation and reflective coatings, these types of coatings are making a tremendous impact on how the world views the best method to insulate buildings, structures, equipment, and transportation sectors. When realizing that the standard insulation materials are only designed to respond to “conduction”, which is only one of the three forms of heat transfer, the coatings can respond to all three of these forms (radiation, convection and conduction). As the demand for saving energy increases and the cost of energy itself increases, the standard forms (fiberglass, rock wool and foam) are being analyzed for what actual benefit they offer versus the newer technologies of using white coatings, and the very latest advantages of using ceramic compounds in coatings for insulation effect.
As realized, the standard insulation materials have always depended upon thickness to promote their effectiveness–the greater the thickness, the better the insulation effect. In actual laboratory testing, temperatures established for the standard materials never resembled the actual world temperatures and, therefore, the results relating to the effectiveness per inch or centimetre were never an exact science. After a certain thickness, the effectiveness drops off dramatically. It was assumed that each additional inch or centimetre of thickness would give the exact additional R value, but this is incorrect.
Following this avenue of understanding, the more thickness added should have given the exact measure of additional R value, but such was never the tested case. Also, the fiber materials require a completely dry environment and no wind since moisture or humidity can load into the fiber to cause the fibers to help transfer the heat at a much faster rate. For fiber materials, the only true heat resistance is in the pockets of air. If wind is present, then this will blow into and through the fibers, which eliminates the heat resistance provided by any air pockets.
Insulation Understanding
What is important to realize is that to accept R value materials as being the only source of insulation materials, means that “conduction” is the only source of heat that you should consider. If 100% of the heat is loaded which is allowed by the standard insulation materials, you are only able to slowdown the transfer of this heat to the cool side. The critical point in this statement is “slow down” the transfer. This means that the standard materials cannot avoid loading 100% of the heat because they do not reflect.
What the “R” value is measuring is the “speed” in which the heat load is transferring through the material. It was never disclosed as part of the R value system to discuss what happens when all of this heat finally loaded the insulation material and once loaded, what did that mean? If the resistance (R) was to slow down the transfer of heat through a material, then you could accept the R value “UNTIL” the material was fully loaded with the heat after it transferred through it. When the material was full of heat, the question is: does it continue to have an R value then? The answer is a diminished value at best. It is full and the heat is simply passing through it at a uniform rate without the initial resistance. This is a standard fact of measurement and testing.
Once a material begins to resist heat and the “R” value calculation is established, the material begins loading heat and the resistance diminishes as the heat increases inside the material. This single extremely important fact is ignored in judging the “R” value of insulation and thickness for use in the field. The “R” value is presumed to remain unchanged when exposed to field conditions, loading of heat and thickness needed to offset these conditions. Physics cannot be avoided. Heat loads automatically and then will equalize across a material into which it is allowed to load.
To reference this point, Georgia Tech University attempted a study on roofing when a ceramic filled coating was applied versus other types of insulation and decided to bring the “R” value measuring equipment outside to do the testing. It was quickly realised and recorded in their documentation that the “R” value equipment can only work in a solid state environment (laboratory) because of the constant changes in climate conditions of wind, temperature and humidity. From this exposure to the limitations of determining an “R” value, how could this value ever realistically be used outside a laboratory in the field?
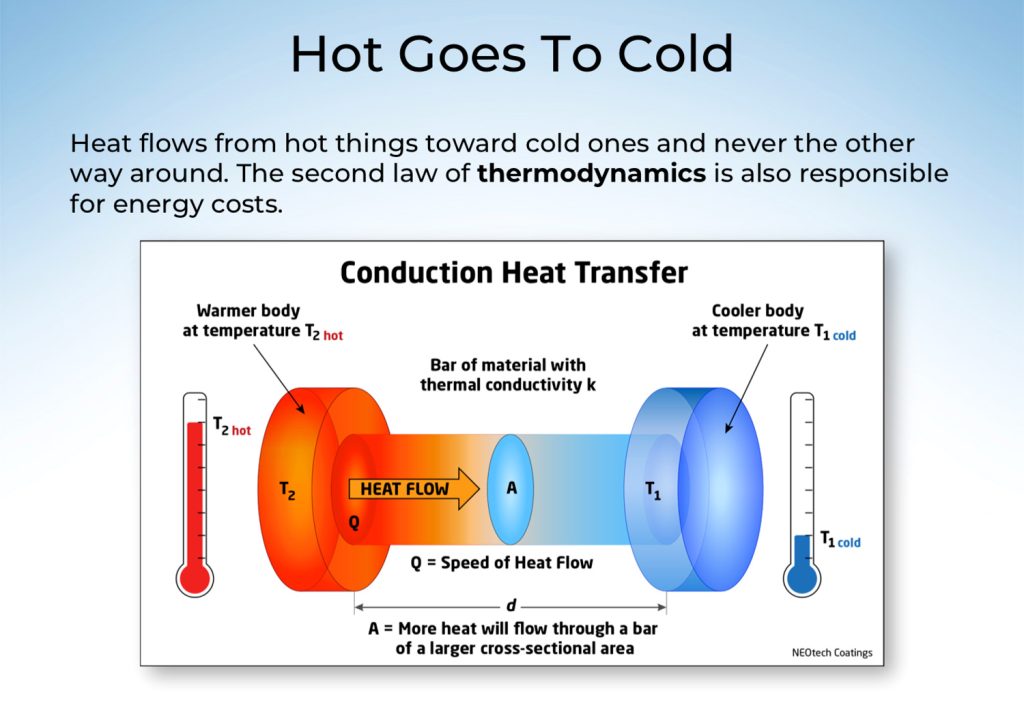
Energy Realisation
When energy became more costly in the profit picture of companies and in people’s minds, it must be a category of cost that can be controlled. At this point, the acceptance of new technologies came to the forefront. Complacency to continue with the standard forms of insulation had to change when it was re-analyzed, and became apparent that it did not work as well as accepted.
Liquid Insulation – First Step
The first entry into the market was white paint showing that when a roof or surface was coated, the white would reflect much of the visual heat or short wave radiation and, therefore, block out a percentage of the initial heat load experienced on surfaces facing the sun. This initial realization that white is used for this purpose in clothing and house color made immediate sense and was accepted by everyone. The problem with this open acceptance was the fact that white paint does tarnish and becomes dirty over only a short time frame from six months to a year.
When the white surface was no longer white, it could not effectively repel the limited source of visual light heat from the surface and the insulation effect was lost or short lived. Also, white paint is very limited in its ability to block out infrared radiation, which represents 53% of the radiation heat from the sun. Therefore, using white paint is effective for only a percentage of the remaining 47% of the sun’s radiation heat, which leaves most of the heat to absorb into the surface and transfer to the cool side.
Understand this point: If white was the only answer to blocking heat load and conduction, then touching any white car hood would feel cool–it does not, and loads much of the heat that radiates to it, therefore, just because it is white does not mean it will reflect heat and insulate.
White is better than other colours to begin the effort to insulate, but alone, it is not the answer. As time and research continued, it was found that by using peralite materials, the reflectivity could be increased over what the Tio2 (Titanium dioxide) could provide and improvements were made to these reflective paints, but still limited by the surface deterioration from dirt and weathering.
Liquid Insulation – Second Step
The next step in technology advancement came with the idea of making actual “insulation” coatings using glass hollow spheres after the Space Shuttle had used glass in making the tiles. This was a great stride forward in finding a better solution to the reflectivity aspect into actual controlling heat loss or gain. When the NASA shuttle was using glass frit (also referred to as glass soldering or seal glass bonding, describes a wafer bonding technique with an intermediate glass layer) to make the tiles to protect the Shuttle from the re-entry heat by allowing the shuttle to skip through the atmospheric layer on a surface of glass surfaced tile, it was thought that the logical leap in technology would be glass beads loaded into any white paint and this would provide an insulation effect even after the coating became dirty or tarnished.
It was soon discovered that using the glass hollow sphere (bead) had to be loaded into a coating to such a maximum level in order to achieve any measure of success, that this caused other problems. When the hollow spheres are loaded to the maximum, they float on top of the resin system within the container and must be remixed to disperse them uniformly inside the container before applying. At the same time, using only hollow spheres allows many of these spheres to be broken during the mixing process. The hollow sphere must be lightweight and fragile to be able to work the most effectively.
If a hollow sphere has a thick walled glass, it cannot work as well to block out heat because the glass will absorb heat and hold it inside the hollow cell. Therefore, the use of only hollow spheres had limitations in design and performance when stirred and broken, than when applied and facing the weathering factor. Since the hollow spheres had to be loaded with such a maximum load level, the resin system used to glue them together or bind the spheres suffered dramatically.
This means that there is not enough glue or resin to bind the hollow spheres together and then be able to provide a strong enough system to be used on roofing to withstand weathering for years in temperature changes, radiation deterioration, and climate variations (wind, rain, hail, salt air). There must be a strong resin system to bind and hold all of these hollow spheres together to withstand the elements and provide longevity. There has not been sufficient long-term data on hollow sphere coatings used on roofing to show history of long term usage.
Where the hollow sphere excelled was in covering over pipes or vessels up to 160°C (320°F) to be sprayed over the surface and to insulate the pipe by holding the heat on the surface of the pipe and providing actual insulation. What is meant by actual insulation is that the heat is actually held on the surface in order to prevent it from escaping off of the surface and lost. The standard insulation materials will absorb the surface heat and then slowly resist the loss of this heat from the surface. Because the coating can be sprayed, it can be applied to elbows and valves no matter the configuration of the unit and provide more complete control against heat loss. The parameter for these coatings is the limited surface temperature that it can cover and the ability to withstand weathering.
New Technology Progression
As technology progressed and continued with the research of ceramics, one company in particular came to the forefront because they have spent 33 years in ceramic research and development. They had found that the term “ceramic” could mean many descriptions and compounds.
To develop a true roof insulation coating, the idea was that the resin system must be designed to be as important to the product as would be the ceramic insulation materials used. To have an excellent insulation is the goal, but if the resin system does not hold it in place, what good would this be when the insulation material fell off? Therefore, a blending of resins was developed that could withstand extreme temperatures and climates with only minor deterioration over 20 years. An example of this concept was presented when this water-based system was applied at 200 microns and after 20 years in a harsh environment, there is 162.5 microns still on the roof after deterioration. This was applied and monitored over this time by Japanese and American groups. This concept of concentrating on the resin system to be effective in all climates over a long period of time is critical in holding the insulation materials in place to provide for long term insulation effectiveness.
The second part of making a true insulation coating based on “reflectivity” was to identify the different types of radiation waves, and then find the particular ceramics in size and crystalline structure that could match up with the vibration of the waves to block the wave effectively from heating the roof or surface it covered. After researching an excess of 4000 ceramic compounds over a 33-year period, 12 compounds were found to work effectively because they matched the radiation vibration to block it or resist the heat load due to low density.
These were chosen to blend into the unique resin matrix for the insulation effect. Four specific ceramic compounds were chosen to catch and block the three main radiation waves from the sun (UV, Sunlight or short wave and IR – Infrared or Long wave). Once these particular compounds were in place to block the heat waves, the coating was assembled that could provide a blocking of heat on the surface of roofing or walls to provide long term insulation effectiveness.
It was important in this selection of components to make certain that the compounds could provide a block to the radiation wave even though the surface of the coating had become dirty and tarnished. In other words, the insulation effect would not be affected by the surface of the coating becoming dirty and having reduced whiteness.
The ceramic compounds would continue to block the vibration of the radiation waves regardless of the weathering effect on the surface. At the same time, the chosen ceramic compounds also had such a low density factor that the physical loading of heat into the compound could not occur. There must be a certain density to a material to allow the heat to absorb and be held before it can be transferred or conducted. The less density in a material, the less amount of heat can be absorbed and transferred.
This was a breakthrough in developing a reflective coating to give options for blocking “heat load” for roofing and walls. At this point, it is realized that all the attention to a “reflectivity number and simple emissivity number” does not directly relate to “heat load”. If it did, the white car hood mentioned above would never become hot, yet it is very hot and will burn your hand. To block the heat vibration of a wave and to have a low density to resist absorption of the heat made the perfect roofing and wall coating that could last for 20 years (proven) and continue to insulate over that time period. At the same time, a blended resin system provided a water barrier film, a “0” flame spread, a mould/mildew barrier and a tested and proven sound barrier from the same coating film of 250 microns (10 mils).
The sound barrier achieved by the same ceramics had such a low density that did not allow for the radiation heat to load, and sound waves could not make these compounds vibrate which diminished the continuation of sound through walls. This coating has been used by major companies to coat the interior ceilings and walls to help hold heat in during winter months while helping to block heat that loaded on the exterior uncoated side from conducting to the interior.
Understand that “facing the heat source is the most effective” way to use the coating, but because the combination of resins that seal a wall also helps in controlling moisture load into the wall to keep the wall dry which helps in any insulation concept. This was used in cases where the exterior could not be coated and the customer wanted the walls and ceiling “sealed” effectively to help with the moisture load and air flow causing loss of heat. The Energy Specialist for a US Energy Authority did three separate tests in three different parts of the US to observe the performance of this coating in blocking heat gain. After the third test result, the official stated that “this was one of the most effective insulation coatings he had tested and was well deserving of the Energy Star Award it had received”.
The calculations from the DOE representative stated that this coating would give a 2-year return on investment (R.O.I.) when applied over conditioned facilities which had the standard insulation materials in place. This coating was again tested by the combination of the Sony Corporation working with the government of Japan and found that the Return On Investment after coating 43,000 sq.m (464,000 sq.ft.) of roofing which already had rock wool installed had a 1.1 year payback on the cost of applying this coating. This coating has passed the CRRC (Cool Roof Rating Council) testing and showed very little loss in performance over a three-year period when retesting was performed to find the continued effectiveness.
This validates the testing from Japan where an architectural company went back to several roofs, coated up to 10 years prior with this coating to check again the heat blocking performance of this coating. They found and substantiated that even though the coating was dirty, as expected, there was no loss of performance on the surface temperature, nor the underside readings under the roof and the temperature readings inside the buildings one meter off the floor. The idea of reflectivity and emissivity of a coating is important but often times misunderstood and misstated.
Emittance is the amount of heat released off the surface of the coating back to the atmosphere which reduces the amount of heat available for transfer through the substrate. Emissivity is based on a black box (1.0) which the emissivity equals the absorption of the heat onto the surface. To have a high emissivity is the best as presented by the CRRC and Energy Star verifications for coatings under the testing criteria. For a company to argue that a high reflectivity and emissivity is the only points needed to prove effectiveness is to show their failure to understand the basics of heat terminology. The coating highlighted in this discussion was tested for a high reflectivity and high emissivity.
The very specific combination of the reflectivity when accounting for all three forms of radiation wave is 95% and then having a high emissivity of .91 is excellent. The heat wave is reflected away while at the same time, the surface heat that is trying to be absorbed in the surface of the coating is being released back to the atmosphere at a .91 rate. The physical make up of this coating is 61% solids by volume by using only ceramic compounds and no fillers to achieve such a high-performance rating. To state again, it is not the level of tested reflectivity and emissivity that determines “heat load”, it is what the coating is made of to resist the initial loading of heat. Reflecting light waves on a test does not directly relate to heat load (remember the white car hood with white paint being a 70% reflector and good emissivity, but it loaded most of the heat).
Environmental Impact & Certifications
The environmental impacts and benefits of Super Therm® is very important and thoroughly tested.
Super Therm® was tested originally by the USDA (United States Department of Agriculture) for use around foods and tested for toxicity around foods and humans. It passed and was granted a letter of approval in 1990.
Super Therm® was again tested for toxicity and environmental safety by the IMO (International Marine Organization) to be used on ships and be safe for all personnel.
Super Therm® was tested by the MBDC organisation to pass all raw materials through a breakdown analysis for use in the general markets around the world. MBDC established a method to analyse all raw materials in a coating product in order to quality it for the US Green Building Council approval for products used to grant structures the LEED (Green Building Certification System) points.
Super Therm® has been accepted into the MASDAR (UAE) system for approved products by passing the required standards. MASDAR is the first city to be designed for construction in the desert that is 100% green.
Super Therm® was tested and approved for use by NASA (National Aeronautics and Space Administration) for Flame Spread under their testing standard NHB 8060.1B/C Test 1 and under their standard NHB 8060.1C, Test 7 for showing no toxicity. This product was cleared to be used on the interior of the Shuttle.
Super Therm® was tested under the ECAP-CUL-1-03 ENERGY CONSERVATION ASSISTANCE PROGRAM for the State of Florida. Testing was performed in Miami, Florida, Denver Colorado and LaPorte, Texas to verify the performance statements and advertising.
Super Therm® meets the standards of the ASHRAE (American Society of Heating, Refrigerating and Air-Conditioning Engineers): 90.1 Code compliance.
Super Therm® is DNV (Det Norske Veritas) approved and the SOLAS 1974 Convention as Amended.
Super Therm® is Factory Mutual approved for roofing and other applications to meet the insurance companies of America standards.
Super Therm® is JISC (Japanese Industrial Standards Corporation) tested and verified under JIS A5759.
Super Therm® is approved under the CSSC (China Center for Technical Testing of Non- Metallic Materials for Ship Building, China Ship-Building Corporation). VOC is less than 100 grams per litre.
Super Therm® has been accepted by the Green Label program in Singapore. “Certified means that an examination of samples of a product or investigation has been performed by the Council to determine compliance with the Guidelines and that permission has been granted in accordance with this Agreement for the User to represent its Product as Certified”.
The developer and formulator for these high tech coatings, J.E. Pritchett has been a speaker for the NACE engineers with Aramco in Dammam, Saudi Arabia, the 12th Middle East Corrosion Conference and Exhibition in the Kingdom of Bahrain and a speaker for the Off Shore Arabia Conference 2010.
Next Break Through of Technology
The next break-through for using ceramics in a coating development was to combine some of the other ceramic compounds from the research into a water based coating that is more complex and loaded. This coating is thicker and specifically designed not to reflect heat but is designed to resist the loading of heat from hot surfaces to be the best insulation for pipes, vessels or equipment where holding heat inside the unit is essential.
Two types of coatings were made to perform this type of project.
First, our HSC® coating was made to have a more smooth appearance in order to be more architecturally acceptable. This coating is designed to raise up to 160°C (320°F) and outperform all other coatings in the market that are using only the principle of hollow glass spheres technology. This coating is designed with seven (7) different ceramic compounds to give a more concentrated effort to resist and retard heat from escaping or dissipating from a hot surface.
HSC® (Hot Surface Coating) can be applied in just a couple of applications or coats, whereas the limited hollow sphere-loaded type of coatings from other companies must be applied in multiple applications to avoid breaking the glass beads and causing the loss of performance. Whereas heat could deteriorate the typical hollow sphere coating, causing it to brown out and flake off in time. HSC® is designed with a series of ceramics that combine with each other to form a matrix to hold the coating together and provide the insulation performance while protecting the resin system. This coating was tested using basic ASTM designed tests (ASTM C177) to compare to the competing similar coatings and outperformed them by 28%.
Not many competing coatings will actually do ASTM testing to produce heat transfer numbers because then they can be compared to this new developed coating – HSC®. Some hollow sphere coating promoters decided to use statements that cannot be validated as “equivalency performance numbers” in order to post R equivalent number and this is totally their own opinion. “R equivalency” can be used, where you do have tested performance as the base. To be very clear, a thin coating cannot have a “R” value because it is not a minimum of one inch in thickness. The “R” value was established specifically for fiberglass in the 1970’s for that type of insulation material. The “equivalency” statement is made to tie it to the only understanding of insulation that most people have.
Secondly, in the industrial fields, most of the hot surface projects on pipes, vessels and valves are well above 200°C (393°F) with many being around 470°C (878°F) and higher. This next coating, HPC® (Hot Pipe Coating) was made from a different selection of the researched ceramic compounds to provide insulation over this temperature along with a specially designed resin system to hold the system to the hot surface without failure. All of this is water-based and non-toxic. This coating is applied while the system is operating and, therefore, avoids costly plant shut downs to apply the insulation – saving time and money. To compare, the hollow sphere coating systems were asked to apply their coating at a side by side test site to prove their glass hollow sphere coating could effectively be applied to surfaces at only 160°C (320°F) at the thickness claimed by their advertising. Details are left out here for sake of time, but these types of coatings cannot perform in these situations.
The new, high-technical, high-temp formula (HPC-HT®) was applied at 470°C (878F) to an operating pipe while engineers watched, and after 30 minutes they were able to lay their hands on the coating surface without burning and able to hold their hand on the surface long enough to prove it did, in fact, insulate and did it immediately upon application.
Nano Particles
The current phase of ceramic study being performed by SPI is the use of nano materials. Nano is largely misunderstood by many in the field of engineering and sciences. The size is 1/billionth of one metre. You should not be able to see a nano by the naked eye unless there is a larger quantity and then it would appear more like a smoke. Scientist have worked with and have known about nano materials for many years, then when nano materials were first introduced to the public in the 1990’s, there was a lot of excitement about the possibilities and what they could be used for. There was also concern about the health issues of breathing in nano materials and what this could do. As the work on nano materials has progressed, scientist have found better ways to control the nano particle to be used safely. SPI is working with scientist to find the correct way to introduce the nano technology into a coating film to perform in ways that will enhance the quality of life, save energy and preserve the natural resources.
Understanding and Due Diligence of Ceramics
Much advertising is in the market as to how someone should evaluate an insulation coating. Either by using some formula, or using standard accepted key terms, or by simply re-stating the principles of Conduction, Convection and Radiation, or by talking about thicknesses, but the main point to performance is application and temperature readings to see the performance.
If companies have not performed due diligence in ceramic compound research and do not understand which compounds work effectively according to either laboratory testing or by trial and error, their statements are only opinions without substantiation. Also, another point that must be considered by a customer is – does a supplier of the coating product actually make the product themselves or do they purchase the product from a manufacturer to resell under their own private name. When coating companies provide only one basic coating that is advertised to perform in all situations, this shows that they do not have any research and development programs and no understanding of how to develop new technologies. This is critical for the customer because new technology is the key to solving problems in the future and the supplier must have the ability to perform Research and Development for themselves to understand how to make new products to solve new and existing problems.
Ceramic compound research is ongoing and the company (SPI) that has already monitored and studied over 4000 compounds will be the company that understands very specifically which ceramics will work and in what performance areas. All other companies in the market that are advertising ceramic insulation or reflective coatings are only guessing and making suggestions about opinions without the same knowledgeable basis.
Ceramic compounds are a science and require hands-on trial and error testing in a laboratory to understand which compounds can perform on two separate levels: Reflectivity of the actual radiation waves and non-absorption, non-conduction of surface heat. This also is very clear that a singular ceramic coating cannot be designed to do all projects for reflectivity and non-conduction. Specific ceramics are designed for specific performances and a coating must be designed to do that specific job.
Additional Technology in Corrosion
There is an additional note about the SPI company that designs the specific ceramic coatings for these projects. This same company also designed corrosion protection coatings in a one-coat system that encapsulates existing rust without sandblasting, as well as using the same ceramic technology to produce fire rated coatings providing a fire rating up to 7 hours.
The specific corrosion protection coating named Rust Grip® was designed due to the lack of understanding by the major suppliers in the market to address the true reason for reoccurring surface rust even when the procedures were followed for blasting and three coat systems. CUI (Corrosion Under Insulation) is the main corrosion problem worldwide. This situation points up a problem with the wrap and jacket insulation systems CUI was created by this system of insulation. Fibre wraps have chorides in the raw material used to make them and therefore given moisture and air inside the metal jacketing, you have corrosion development.
Because corrosion over surfaces was not being controlled by the standard blast and three coat system, Rust Grip® was developed in the field to be applied directly to the rusted surface or only commercially blasted surface and applied as a single coat system to provide primer and top coat all in one application. Only if colour was needed would a top coat be needed. If pack rust or build up was present, the commercial blast would be used to clean the surface and knock this down to surface rust before application.
The Rust Grip® is designed to do what the other systems failed to do, penetrate deep into the pores of the metal or surface rust, then absorb moisture out of the atmosphere to cause a reaction gassing effect to swell and fill the pores and bottom of the surface rust to encapsulate and smother out the air and moisture. When the pores are encapsulated and cannot breathe nor absorb moisture, future corrosion development is now controlled. At the same time, the Rust Grip® was designed to strengthen to 6780psi surface tensile strength to withstand abuse. Plates were submitted to test labs applied over steel, applied in one coat at 6mils dry film thickness single coating, no top coat, and performed for 15,000 hours (30 years) in the ASTM B117 with a perfect 10 score. Rust Grip® has been tested at Carderock Naval Sea Systems Command and is accepted as a corrosion control coating.
Conclusion on Viewing Technologies
SPI (Superior Products International II, Inc.) has the priorities in the correct place. To identify problems and design coatings that can manage and solve problems. Advanced Continuing Technology is what industry needs, and associations with raw material companies that provide the latest in new technology is where SPI is positioned. If insulation or coating companies only offer a limited source or type of coatings to solve problems, then they are limited in their technologies no matter how large they may appear to be or how many colours they offer.