Different Heat Reduction Coating Compounds Compared
To understand how “heat” compounds react to all three heat nanowaves of infrared, UV and visual heat helps understand what it takes to be a true, high performance thermal coating. In reality many compounds rely on being white to mostly reflect visual heat which is 44% of total solar heat or they say scatter, reflect etc so it’s all in the language and test results.
There are different types of compound references including hollow spheres, various minerals and ceramics that are used, advertised and promoted as ‘the best at reflecting heat to cool buildings’. Its important to address these compounds so you understand what they are and how they benefit the goal of blocking heat load which is cost effective, reduces energy demands, reduces CO2 emissions and provides a safe living standard for humans as part of the ‘cool roof’ movement.
Most of the heat reflective paint testing and summaries do not address the purpose of “loading of heat” and addressing all the heat nanowaves, yet may discuss emissivity and reflectivity. What many of these compounds don’t address either is when they get dirty the life of the product is reduced and its heat reflective efficiency is diminished.
The key words products use include scattering, refractive or reflective. There is no definitive answer in these words for exactly how much heat is being blocked. Therefore the concept of cooling is always inferred, never directly answered. How many watts of solar heat are being transferred is paramount information.
Separating heat reflective paints from true thermal heat block coatings is vital. If a white paint coating is placed on a rooftop and compared to a normal black roof, does that mean it provides thermal heat block capabilities? Not really, it solely means that the coating is providing a reflective function based visual heat from the white and, therefore, lowering temperatures into the roof. Yes, from a different point of view it might be construed as “insulation” but in reality, it still is simply reflecting some solar visual heat prior to its entry into the roof only based on how ‘white’ it is or it’s albedo. The question is…
Do any of these compounds or formulations show any evidence how they block infrared heat or reduce watts of energy transfer?
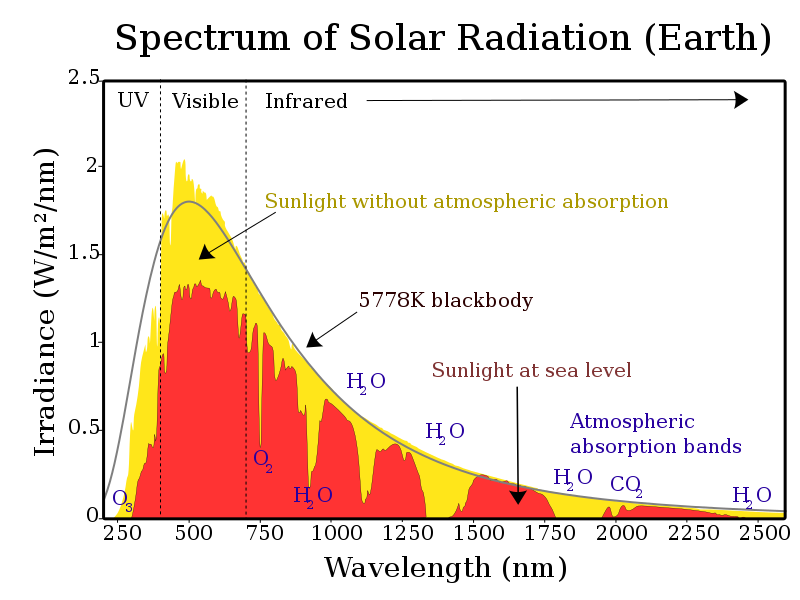
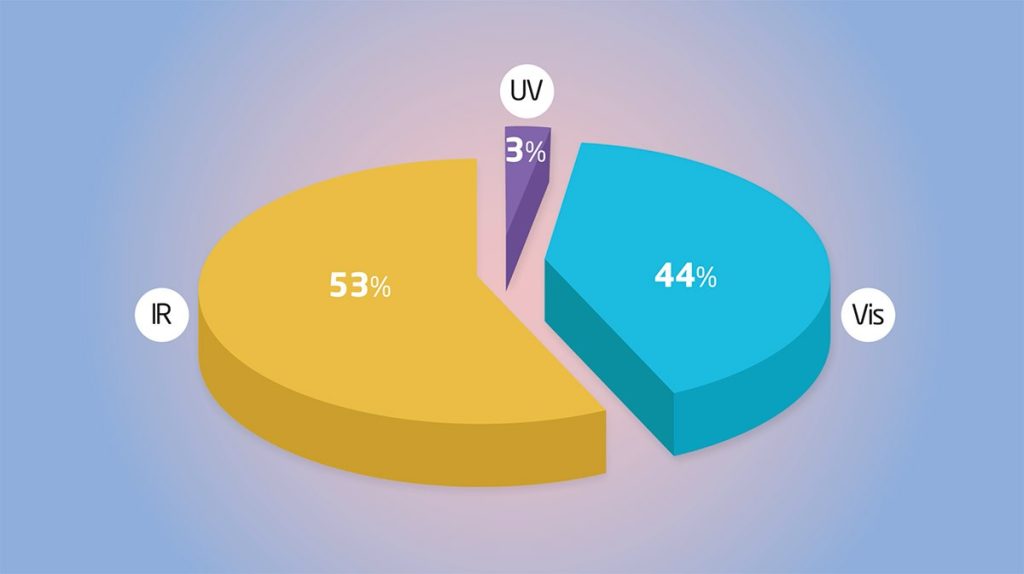
Hollow Spheres
Hollow is the key for these spheres or bubbles to work. They are made in several ways but usually are made by high heat cooking of a material until it reaches temperatures that cause it to form bubbles that float up and screened off into different sizes. Many advertise that these bubbles are vacuum sealed and are the best. As the same as when vegetables or fruits are being canned and the container is hot, then as it cools the air inside condenses and pops the lid down tight. That is the “vacuum” taking place. Not some exotic vacuum system being placed on the bubbles individually. Therefore, it is simply an air vacuum when it cools that is only air and nothing more.
Others state that a ceramic-based additive for paint that helps reflect radiant heat which are a blend of microscopic hollow ceramic spheres. When the paint dries, these little spheres pack together, making a tight layer with increased reflectivity. Just adding random hollow spheres to paint or texture mixes won’t block the infrared heat. If you understand that heat nanowaves are a specific size, heat will simply transfer through and create heat load.
Over 30 years all sizes of hollow spheres have been tested individually to see if size, wall thickness (crush strength) had a particular play in the performance. It does. Usually the lighter density or the least crush strength offered the most insulation ability of blocking the initial heat load and transfer of heat. There are some smaller size that can be used to fill into and between the larger ones to help fill the gaps to make this hollow sphere system work best. This is not a set in concrete type of mix level and depends on which hollow spheres are being used together. If densities are different, this does not settle out well when applied.
Guesswork comments how heat works from an online forum: The “magic” ingredient is glass microspheres. The infrared hits the paint, bounces around inside the spheres and changes wavelength to a length that is readily reradiated by white paint. Turns out these are readily available at fibreglass shops. Mix into your preferably white paint of choice until it’s sludgy. Apply to your prepared surface with a brush, roller or an underbody spray gun. It’ll have a reasonably rough texture so seal with a coat of straight paint.
All in all, hollow spheres can be one of several strategies used for the initial thermal blocking on a surface. You must remember that hollow spheres are filled with air, air does heat up in short order and your dependence on only hollow spheres eventually fails during the day due to loading heat itself. Like bulk insulation filled with millions of tiny air gaps, eventually the heat travels through.
Any claim about “vacuum beads” as a key feature, immediately raises concerns. Hollow spheres, regardless of type, are produced in high-temperature furnaces. During the process, glass beads form, rise, and are separated by size and wall density before being packaged. As these beads cool, they naturally create a slight vacuum, similar to how a jar of cooked vegetables seals as it cools. This is a routine process, not a groundbreaking innovation.
Companies appear to present the commonplace phenomenon as something proprietary to attract less-informed buyers. However, the true performance of hollow spheres in insulation coatings lies in the thickness of their walls and their ability to block heat—not in the small vacuum created during cooling.
The claim that “nano-sized” beads are superior for insulation is misleading. Effective insulation relies on hollow spheres being large enough to trap sufficient air. Nano-sized beads are too small to create functional air pockets, rendering them ineffective for this purpose. The assertion that “nano beads offer a million times more beads” is irrelevant if those beads cannot perform as needed. Larger, light-density beads are far more effective in insulation applications.
Additionally, nano beads present significant challenges in coatings. They are hydrophobic, meaning they do not integrate well with water-based coatings and tend to separate, rising to the surface and potentially dispersing. This makes them impractical for insulation coatings. Buzzwords like “vacuum” and “nano” may sound impressive, but they offer no real value in this context unless applied appropriately—and this is not the case for insulation coatings.
Credible claims require credible evidence. Always look for independent government testing to verify product performance. The absence of such testing is a strong indicator that the claims may not hold up to scrutiny.
Calcium Carbonate
Calcium Carbonate offers tremendous brightness. We encounter calcium carbonate for the first time in the school classroom, where we use blackboard chalk. As stated in the calculation of reflectivity and emissivity, do not be fooled by white surface reflectivity and a high emissivity that does not account for actual heat loading. Also, just like any white surface, it can become dirty over just 6 months and drop performance. Does any advertising of reflective paints in the market ever go back and give you 1 year, 5 years, 10 years and beyond performance data. Is it still working as reported on day one when nice and white and clean? We’re not talking about the coating being still on the roof after 6 months to 5 years. We’re talking about checking the top surface temperature of the coating and then the underside of the roof temperature to prove performance is continuing. No results go back to show how well they are working “after” applied…or 5 years later not to mention the potential of peeling, flaking or cracking.
Barium Sulfate
SPI tried Barium Sulfate long ago when J.E. Pritchett worked with NASA in doing the study on ceramic compounds. It was noted it helped but not that much as you must “load” the coating film very heavy with Barium Sulfate to work. If the surface is loaded too much with Barium Sulfate it will not adhere to the surface and crack – like a dried river bed. Barium Sulfate (BaSO4) is a white, heavy insoluble powder that occurs in nature as the mineral barite. Almost 80% of world consumption of Barium Sulfate is in drilling muds for oil. It is also used as a pigment in paints, where it is known as blanc fixe (i.e., “permanent white”).

In an article from Purdue University, the second feature of their new white paint is that the Barium Sulfate particles are all different sizes in the paint. How much each particle scatters light depends on its size, so a wider range of particle sizes allows the paint to scatter more of the light spectrum from the sun. “A high concentration of particles that are also different sizes gives the paint the broadest spectral scattering, which contributes to the highest reflectance,” said Joseph Peoples, a Purdue Ph.D. student in mechanical engineering.
Like sound waves, heat nanowave lengths must be met to block the heat from a particular wave by matching the sizes. Having different sizes helps in controlling the passage of heat through a coating film. If you have (by using different sizes) all the voids between particles filled in, inside the coating film, the heat has a more difficult time in transferring from hot to cold side.
When compounds are promoting as ‘sends infrared heat away from a surface at the same time‘ this is in context of emissivity. Emissivity is the ratio of conductive infrared heat that is absorbed, equalised and then released in comparison to a blackbody. So black absorbs the most amount of heat, equalises and emits it back out. A coating or paint that releases infrared heat is just emitting what its absorbed and loaded.
The article continues, the paint’s whiteness also means that the paint is the coolest on record. Using high-accuracy temperature reading equipment called thermocouples, the researchers demonstrated outdoors that the paint can keep surfaces 19°F (10°C) cooler than their ambient surroundings at night. It can also cool surfaces 8°F (4°C) below their surroundings under strong sunlight during noon hours.
This is the core difference with claims of the whitest paint which relies on reflecting light but not blocking infrared heat, they need 2 different paints. It’s all-in-one with Super Therm.
Shane Strudwick, NEOtech Coatings
A Fast Company article highlighted the truth of the world’s whitest paint. On roofs, certain coatings – like the world’s whitest white paint – can reflect light into space, but the same coatings don’t work as well on walls because they’re exposed both to the cool sky and to heat that reflects from hot pavement. “These two directions require different properties for cool walls,” says Qilong Cheng, a postdoctoral researcher at Purdue University who worked on the study as a graduate student at Columbia University. “So we have this two-surface zigzag design, with one surface facing the sky and the other facing the ground.” By coating each surface with a different material, the wall can stay as cool as possible. You can do any surface, in any direction with Super Therm as it both blocks the infrared heat as well as reflects the light.
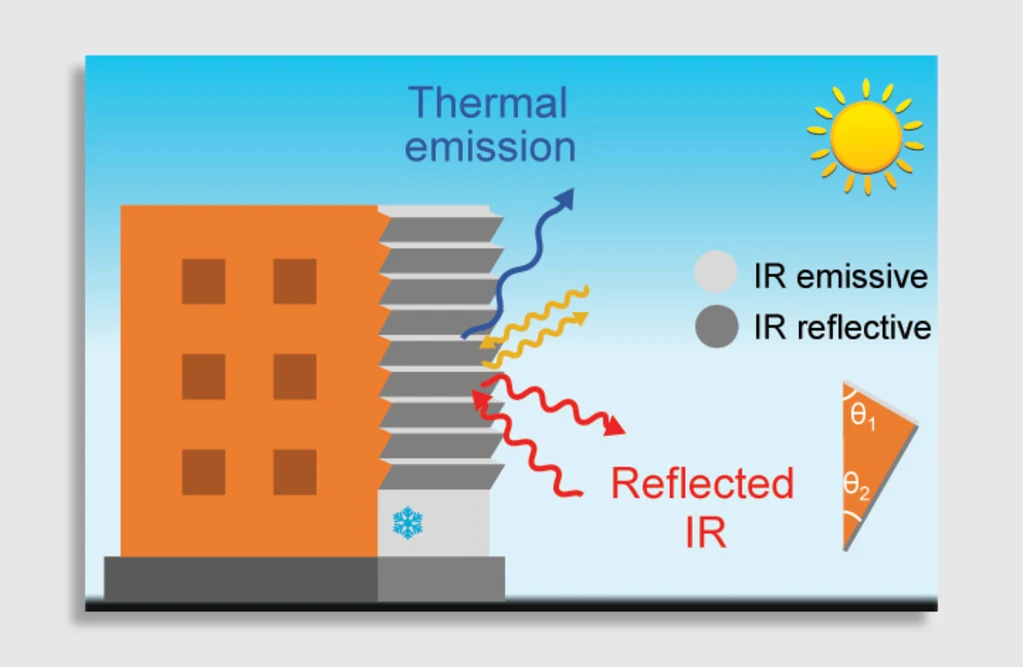
The image above isn’t accurate. IR emissive is heat released off the surface but it still absorbs IR heat and transfer inside. Solar reflectance is not about heat; it’s about light. Light is converted into heat depending on the colour of the surface. So they are depending on reflecting white light, claiming to the be the whitest. Yet infrared heat from the sun is 53% of the total heat. Reflected IR is actually IR blocking. The “whitest paint” can’t block infrared heat. Super Therm blocks 99.5% of the infrared heat from 367 BTUs to 4 BTUs as well as has solar reflectance!
Titanium Dioxide
It has been stated that Titanium dioxide (TiO2) is the most important white pigment used in the coatings industry. It is widely used because it efficiently scatters visible light, thereby imparting whiteness, brightness and opacity when incorporated into a coating. Titanium dioxide is commercially available in two crystal structures—anatase and rutile. Rutile TiO2 pigments are preferred because they scatter light more efficiently, are more stable and are more durable than anatase pigments. It is inappropriate to equate superior performance of TiO2 pigment in paint with high TiO2 analysis. TiO2 is often related to Refractive Indices (R.I.) for pigments used in the manufacture of paint. It’s important to understand that there is a difference between refractive, reflective and blocking.
Titanium dioxide reflects most visible and near-infrared light well, but it absorbs ultraviolet rays, while it’s stated the polymer binder can absorb near-infrared light. This causes some heating under sunlight, so the paints don’t work very efficiently under harsh, bright sunshine (source).
So researchers look to replace the titanium oxide with inexpensive and easily available ingredients such as Barite, which are natural pigments used in paints, coatings and powered Teflon. These compounds help the paint reflect ultraviolet rays. The researchers also reduced the concentration of the polymer binders, which allegedly further reduce the heat absorbed by the paint.
Barite
Barite is the primary, naturally occurring, barium-based mineral. Barium, atomic number 56, derives its name from Greek and means heavy. Barite is also known as baryte, and in Missouri is known as “tiff”. Barite’s high density and chemical inertness make it an ideal mineral for many applications. Compounds like Barite have no proven heat blocking capacity. Yet these articles talk about swapping titanium dioxide for Barite to improve UV absorption.
Amorphous Silica
When a company states they have ‘a groundbreaking heat-rejecting ceramic’ and it’s Amorphous silica…it’s not groundbreaking. We absolutely know that not one ceramic compound blocks all the nanowaves of heat. Super Therm® has 4 different ceramics for UV, visual, infrared and emissivity heat blocking.
Amorphous silica is commonly used in insulation coatings due to its good thermal insulating properties. Amorphous or noncrystalline silica is silicon dioxide (SiO2) that does not have a crystalline structure. Amorphous silica can be naturally occurring or synthetic, and has a wide range of applications. The chemical structure and chemical, physical, and particulate characteristics of amorphous silica are given.
When amorphous silica is in a dry state, it retains its inherent thermal insulating properties. These properties are based on its low thermal conductivity, which inhibits the transfer of heat. As a reference point, the thermal conductivity of pure amorphous silica can range from approximately 0.02 to 0.03 W/(m·K) at room temperature. However, many compounds aren’t the same in dry to wet to dry state.
When incorporated into a paint or coating formulation, amorphous silica is typically mixed with other ingredients to create a uniform mixture. During this process, the silica particles are dispersed throughout the paint matrix. Then the thermal properties diminish yet are being promoted as if they have low thermal conductivity.
Once the paint or coating is applied and dries, the amorphous silica remains within the coating matrix. It continues to provide thermal insulation by reducing heat transfer, similar to its behavior in a dry state. However, the effectiveness of the insulation may be influenced by the thickness and uniformity of the coating, as well as the quality of the application.
Overall, while the fundamental thermal properties of amorphous silica remain consistent whether in a dry state, incorporated into a paint or coating, or dried after application, its performance in a specific application may vary depending on various factors related to the coating system and its application.
Sodium Borosilicate Microspheres
Glass microspheres are hollow thin-walled glass microspheres composed of sodium borosilicate glass. To the naked eye they resemble a fine, white, free-flowing powder. However, magnification reveals them to be near perfect spheres.
In recent years, composite materials containing hollow glass or ceramic microspheres have attracted considerable attention. These materials have very good heat-insulation characteristics, which are largely defined by special features of absorption and scattering of thermal radiation by thin-walled hollow particles (German and Grinchuk, 2002; Dombrovsky, 2005). The paint coatings containing hollow glass microspheres have already found applications for reducing heat loss from the walls of buildings owing to a decrease in thermal radiation at night. Nevertheless, choosing the best disperse composition of microspheres for use in building paints and other polymer coatings remains a problem which requires theoretical and experimental investigation (source).
Hollow Glass Microspheres are high-strength, low-density additives made from water resistant and chemically-stable soda-lime-borosilicate glass. These hollow glass microspheres offer a variety of advantages over conventional irregularly-shaped mineral fillers or glass fiber. Their spherical shape helps reduce resin content in a variety of applications. They also create a ball bearing effect that can result in higher filler loading and improved flow. In this research, amine terminated hollow glass microspheres were prepared by adopting three different routes (source).
Aluminium Alkyd
Features:
- Ultraviolet light resistance
- Long Term Protection against weathering
- Heat reflective
- Resists discoloration
- OTC compliant color.
Testing Properties:
- Adhesion to 200psi
- Abrasion Resistance 180mg loss
- Direct Impact 40 in lbs.
- Dry Heat Resistance 400F
- Exterior Durability 1 year at 45degree South – good
- Flexibility 180degree bend – good
- Moisture condensation resistance – 500 hours – good
- Salt Fog Resistance 500 hours – good
- Thermal Shock – 200 cycles – excellent
- VOC – 458 g/L
Prep: Below 200 F SP 6 commercial blast and SP 1 solvent wipe down. Above 200 F SP 10 White metal blast
Proposed Use: To give reflectivity or some insulation ability by using reflectivity from the aluminium pigment and to help with corrosion control.
What it actually does: The reflectivity deteriorates within six (6) months after initial application due to weathering and fade. The surface will absorb and load heat which transfers to the interior. As to corrosion protection, it does work well for this ability but is affected by the heat load which can crack and peel the coating over time.
Ceramics and Super Therm®
In the beginning since the 1970s and 1980s, the reflective coating concept was very interesting in that using a single ceramic component to reflect surface heat from sun radiation was thought to be the best way to solve heat load. Within a couple of years, this idea that surface reflection would solve any heat load problem on surfaces was discovered to be wrong due to the fact that the coating would become dirty and stop reflecting.
As the established reflective companies continued to promote and sell this technology, J.E. Pritchett visited with his Uncle that worked at Red Stone in Alabama that was connected to NASA. He in turn guided him to the engineers that developed and designed the tiles for the shuttle. In working with these engineers for a short time, J.E. found that the ceramics used for the tiles would not work in a coating product when the environment of the compound changed drastically from dry to wet and mixed with other compounds.
Since 1989, Superior Products International II., Inc. have specialised in ceramic technology. J.E. has been devoted to testing compounds of all kinds (inorganic and organic including ceramics) to see which ones show performance characteristics whether wet or dry and then in combination with other compounds showing these characteristics.
In his studies with NASA Space Agency from 1989 to 1995 when ceramic compounds were taken individually or one-by-one to test the “dry” compound as to how well it can reflect heat, while maintaining its’ level of emissivity to throw off this surface heat to the atmosphere, was the key to long term performance. Then the same compounds were incorporated into a paint formula making it wet and mixed with the usual paint ingredients, question was how well does it continue, if at all, to reflect and have good emissivity.
It was effected and was amazing how much change or percentage drop the reflectivity and emissivity had if made into a paint formula. This is where we see the “general statements” about ceramic compounds being able to reflect heat and have good emissivity all at the same time based on totally untested assumptions. We tested thousands of compounds, over many years and none of this one-on-one testing of each compound is published anywhere, the individual performance characteristics of each compound are not published. Therefore, none of this research is known by the engineering community. Our experience is that if no testing is published, then none of the research is valid and cannot be supported by chemistry or engineering because they cannot validate the results.
The six years spent with NASA is documented, but not a single firm wanted to spend the time and money on testing one compound at a time to find the ones that would work. Like Graham Bell, from over 4,000 compounds tested we had thousands of failures before finding the success. No firm will pay someone to do this which makes this type research unique and very solid. Testing compounds one-by-one to prove or disprove the performance value is the only way to know for sure.
Since none of this type of information could be found in any research books, J.E. began to develop and set up Trial and Error procedures to test ceramic compounds in a base coating. The initial thought was that this would take 6 months and the compounds could be found to perform as planned and the coating completed. In the first 6 months, the initial sources were found. The first year, more sources were found. In the fourth year, it was finally decided what to look for in density, crystalline structure and material compound.
It became clear early on that a single compound cannot provide the performance characteristics alone to address all three heat nanowaves and provide long term performance. Without this study (whether published or not) established the type of kind of compounds that when combined, will perform as needed. These combinations have been used in Super Therm® on a study for over 35 years showing performance. This is the dynamic of a true solar thermal heat block coating.
Rethinking ceramic coatings
Finding the right compounds that will continue to block heat when formulated into a coating is the result of 30+ years of R&D to find individual compounds combined together to form a matrix to block radiation waves and detune signals to achieve reduction in “initial heat loads”.
30 years of ceramic coating success
After 30 years and over 4,000 ceramic compounds, it was found which compounds actually do work in any environment, mixed with other compounds that will improve the performance, which compounds are good for radiation heat in the ambient atmosphere, which work over high temperature surfaces to block and hold heat and which are good for fire control.
Research with NASA performed over a six years period from 1989-1995 culminating in J.E. Pritchett being invited as a speaker on Super Therm in the NASA Technology Conference (Chicago 1995) as a new technology insulation coating.
The next big buzz…Super Cooling and Radiative Cooling Technology
What is Passive Cooling?
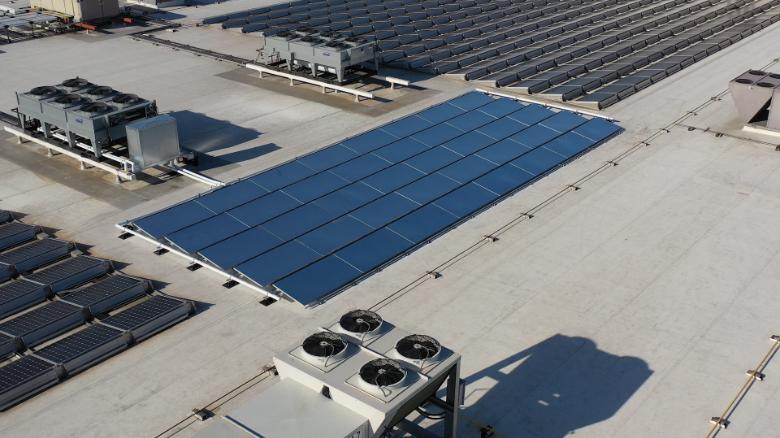
Passive cooling is basically cooling that doesn’t require a mechanical device. You can cool your home with air conditioning, but passive cooling allows you to take advantage of your climate to cool your home. Even if you require occasional air conditioning, passive cooling can help slash your energy consumption (source).
Radiative cooling (RC) is attracting more interest from building engineers and architects. Using the sky as the heat sink, a radiative cooling material can be passively cooled by emitting heat to the sky.
Passive Radiative Cooling is a natural phenomenon that generally occurs at night in nature because all nature materials absorb more solar energy during the day than they are able to radiate to the sky. At night, the surrounding environment cools the material to a temperature that is below the dew point or below freezing to form frost. This explains why you may see frost on your car windshield in the morning, even after the air temperature is above freezing. Passive Radiative Cooling (PRC) reflects enough solar energy to allow passive radiative cooling to occur during the day (source).
However the cost of this cooling film technology is much higher than standard cool roof paints. While radiative cooling technology can have merit, radiative cooling is based on a film and requires infrastructure like solar panels (see above) so the ability to take a standard roof, tiles or other roof assets and apply would be almost impossible. Cool roof paints cover all the roof and assets including air conditioning ducts so this solution really has very minimal benefit. There’s no evidence on the longevity of the films so many questions still revolve around this strategy Read more >
Substantiation
Ensure the manufacturer or dealer produces substantiated documents or testing supported in their technical data. Make sure that the data is registered to the company that made the coating. If the documents are not registered to the manufacturer, then you are probably looking at a private label brand.
Where is it Manufactured?
This is important as many of the insulating coatings and reflective roof paints have many tiers and could be private labels. Typically, if you can find the manufacturer, you have found the real information resource. Some marketers run off of pirated data and use it for their own “private label.” These companies normally are the ones that will over state the results, as well as the marketing to look “really” impressive. Fortunately Super Therm® is manufactured by Superior Products International II., Inc. in the USA. Super Therm® is never produced under any other labels so you’re guaranteed ISO 9001 standards and results.
Heat Block Conclusion
This document is not to downplay any insulation materials or compounds. It relates to how materials work to block heat, reflect heat, resist heat and the concept of emissivity and solar reflectivity and how these materials work alone to try and do the job. There must be a combination of materials to get the best thermal performance trying to fit all angles of heat “load” and transfer.
There are a large variety of compounds and materials in the market that can have some benefit towards reflectivity and some towards emissivity. Alone, they have been found to be questionable or simply inept at controlling all the complete range of heat waves and giving durability or longevity. As we’ve explained, do they show test results, do any of these compounds or formulations show any evidence how they block infrared heat or reduce watts of energy transfer in their testing? If no, then be dubious. Knowing how much energy transfer penetrating past the coating into the substrate is the only way to measure heat load and effectiveness. Super Therm® at just 0.25mm is 0.559 W/m2/K is an outstanding benchmark.
Coatings like Super Therm® have all the verified testing results and field studies including a US Energy Authority based on a proven combination of ceramics which deliver the thermal barrier you need to neutralise solar heat.