Lead Based Paint Abatement and Encapsulation at Fort Bragg
Simmons Army Airfield – Fort Bragg, North Carolina
Products Rust Grip® and Enamo Grip®
Rust Grip® Encapsulates Lead-Based Paint, Asbestos and Rust
No Sandblasting Required or Lead Dust Containment issues
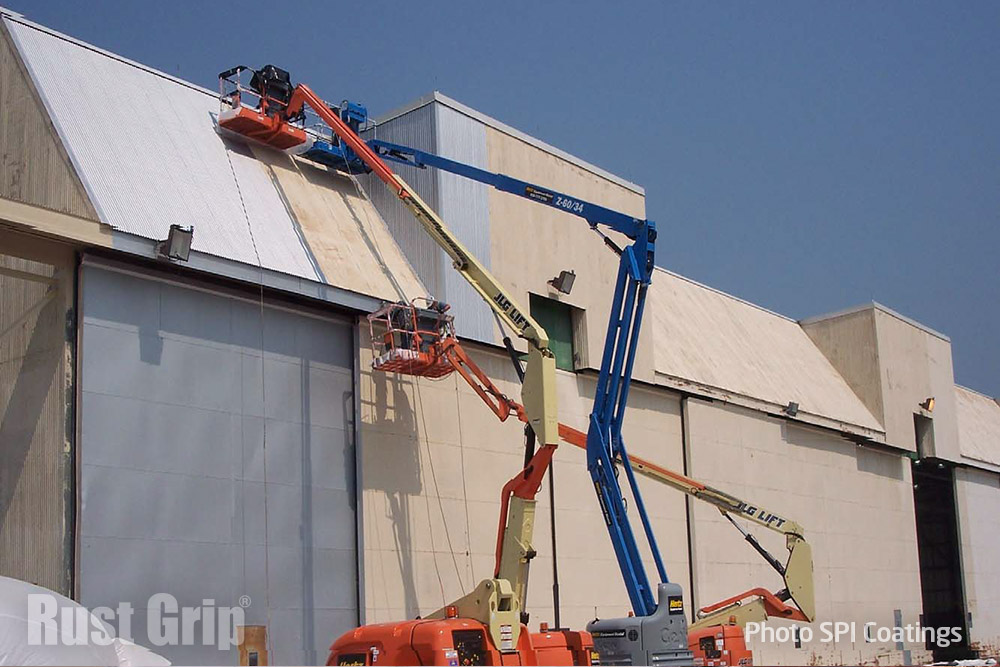
The United States Army Construction and Engineering Research Laboratory (CERL) contracted with Manta Industrial, Hammond, IN to conduct field demonstration and implementation of a cost-effective lead-base paint encapsulation procedure for the protection of steel structures, such as hangars, tanks, and bridges that contain lead-base paint using Rust Grip®. The maintenance and lead base paint encapsulation procedures include surface preparation, environmental protection requirements and paint application.
Rust Grip® is patented (Patent #5,695,812) as an effective abatement method of bio-hazardous material including lead-based paints, asbestos and rust. Rust Grip® is a moisture-cure urethane coating with special additives and resins. It is these additives and resins that separate Rust Grip® from the other moisture-cure urethanes and allows it to be applied directly over existing, firmly bonded paint or rust without any loss of performance. Since the greatest expense in the coating of lead-base painted steel structures comes from the surface prep (abrasive blasting, etc.) and the containment of that residue, Rust Grip® will greatly reduce the overall costs of the project. Rust Grip® was developed to withstand the harshest environments and has a history of excellent performance.
The Problem
Lead-based paints (LBP) and primers have been used in the past by the Department of Defense (DoD) to protect steel structures from corrosion. LBP abatement and disposal is problematic because the removal of this paint creates hazardous dust and waste.
The DoD owns about 2 billion sq ft of buildings coated with some lead-based paint and about 200 million sq ft of steel structures coated with lead-based paint, such as aircraft hangars, tanks, and bridges. The Army owns 95,400 target facilities in the United States and 26,200 in foreign countries. The average age of these structures is 36 years; 90,000 were built before 1978 and probably contain lead-based paint. Furthermore, about 2600 of these facilities are on or eligible for the National Register of Historic Places, and require special procedures for preservation.
The removal of LBP is generally performed by abrasive blasting and abrasive blasting creates its own environmental hazard. Containment and disposal of surface preparation debris, worker protection, and other regulatory compliance costs combine to make removal of LBP very expensive. The residual waste from LBP removal often contains enough lead to be considered a hazardous waste, thereby requiring special handling and disposal.
The Simmons Army Airfield at Fort Bragg contained numerous steel structures such as water tanks, bridges, aircraft hangars, antennas, ladders, poles, railings, catwalks, fire hydrants, fuel storage tanks, and metal buildings were constructed or installed with lead-based coatings. The removal of lead-based paint from steel structures is currently accomplished through a variety of methods, the most common being abrasive blasting which brings many issues such as containment and public safety along with noise and additional cost.
Prior to recoating steel structures, abrasive blasting is required in order to remove the old lead-based paint and to provide adequate surface profile for bonding the new paint to the substrate. During abrasive blasting, a tight containment structure is required to prevent lead dust from contaminating air, soil or water. Inside such containment structures, increased worker protection is required due to high lead dust concentrations. The large, concentrated volume of waste generated by abrasive blasting is hazardous and requires additional stabilization treatment prior to disposal.
Rust Grip® was introduced as a vital strategy to eliminates sandblasting and safely container the lead paint along with the dramatic reduction in cost for the projects on the site. See the full Department of Defence Report.